Well, finally, glassing and subsequent coats are complete. Sometimes schedule drives process and that proved to be the case this time. I ended up doing a coat a day, sanding in between. Hopefully it'll all stick together. Karen did a great job mixing and keeping track of "time until squeegee".
The wet out coat went well. I chose not to seal coat. We did a small sample test wet out with scrap to get an idea of timing. I'm really glad I didn't try to wet out the football at the same time. I do have a couple of spots that if you know just where to look there are subtle shading differences, I presume from not advancing the wet edge quickly enough? I didn't have any trouble with air bubbles or out gassing. Temps were steady in the mid 70's. I used DogBrain's trick of taping out the football, wetting to the tape and trimming the excess glass afterwards. Having started stripping at the waterline made knowing where to tape easy.
I babysat the football cure which reached a point where I could lift the tape back to the football edge and cut the excess off at the fold with a sheetrock knife.
The next morning I tried to feather out the football edge with a new, sharp, tool steel scraper. I made it about a foot before giving up and running to the hardware store for a carbide scraper, which worked well. S glass scrapes way harder than E glass.
The first fill coat went on easily. For the final coat I decided to try an 1/8 inch foam roller. I was so excited at how quickly and easily that worked that I neglected to check frequently enough for bubbles. Too late to tip off, I saw lots and lots of tiny bubbles.
The next morning I sanded everything and recoated with a roller again, but tipped off with a brush as I went. In hindsight, I'm not sure the 4th coat was necessary, but I decided to play it safe. The bubbles were extremely small and not very deep. I guess I didn't want to risk sanding into the cloth, so chose to play it safe.
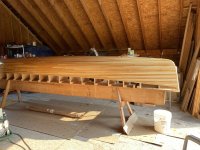