- Joined
- Aug 10, 2018
- Messages
- 1,710
- Reaction score
- 2,554
Coming soon to a garage near me... Round 2 starts next week. This time I'll be looking for a bit more maneuverability in moving water and, as this boat is destined to ply some waters favored by Memaquay, it seemed fitting to trust his judgement and build his preferred hull.

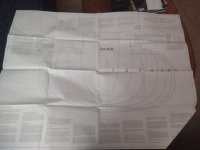
This time, I'll be building a Raven; a John Winters design that I purchased from Martin Stepp at Green Valley Boat Works. The hull will be Tamarac (aka Eastern Larch locally) with Sassafras trim. To offset the heavier weight of Larch (37 lbs/cubic foot) compared to Western Red Cedar (23lbs/cubic foot), I'll, again, be building with 3/16 in strips instead of the traditional 1/4 inch. As this (37lbs x .75 = 27.75 / cu ft equivalent) still leaves me about 20% heavier than the Cedar, I'll be seeking ways to lighten the build and I hope to finish out at or below 50 lbs. (This is a deeper hull than my Freedom Solo which tipped the scales at 45 lbs so I'm prepared to miss the weight goal).
One thing that I neglected to do last time was to keep track of the hours and total cost of the build. I'm unsure I can detail total cost as I still have a gallon(ish) of epoxy left from the Freedom but I hope to be able to punch the clock a little more diligently and track the time investment a bit more closely.
I've got a ton of commitments demanding time and attention through the weekend but I should be milling strips on or before Feb 1st with a tentative (Canadian) launch date of June 30th (it won't break my heart to test it locally prior to that).

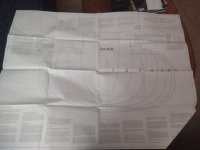
This time, I'll be building a Raven; a John Winters design that I purchased from Martin Stepp at Green Valley Boat Works. The hull will be Tamarac (aka Eastern Larch locally) with Sassafras trim. To offset the heavier weight of Larch (37 lbs/cubic foot) compared to Western Red Cedar (23lbs/cubic foot), I'll, again, be building with 3/16 in strips instead of the traditional 1/4 inch. As this (37lbs x .75 = 27.75 / cu ft equivalent) still leaves me about 20% heavier than the Cedar, I'll be seeking ways to lighten the build and I hope to finish out at or below 50 lbs. (This is a deeper hull than my Freedom Solo which tipped the scales at 45 lbs so I'm prepared to miss the weight goal).
One thing that I neglected to do last time was to keep track of the hours and total cost of the build. I'm unsure I can detail total cost as I still have a gallon(ish) of epoxy left from the Freedom but I hope to be able to punch the clock a little more diligently and track the time investment a bit more closely.
I've got a ton of commitments demanding time and attention through the weekend but I should be milling strips on or before Feb 1st with a tentative (Canadian) launch date of June 30th (it won't break my heart to test it locally prior to that).