Despite falsely accusing me of soiling his garage door and garbage barrel handles with epoxy, Mr. McCrea does have a good side to him.
Some time ago, during a shop day with him he gifted me a clever little idea for a better seat drops than what you typically see on Old Town Canoes.
Having to hang around today for a repair man to show up and do some work for me seemed a perfect time to tackle this little project.
Here's a photo of the standard drilled dowel drop on top of the replacement mini-truss drops. The new drops look like they will seriously help inhibit seat sway.
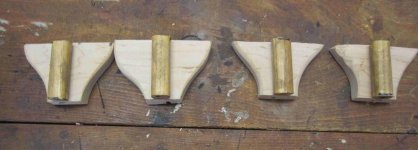
New drops laid in place. As crafted, they are a little too long for my preference. I like about 9.75 inches of seat clearance to more easily get my size 11s under the seat when I kneel. I'll need to take off 5cm to get the drop height I want. It took about 30 minutes of futzing around before I could figure out how to really secure the piece and get a electric scrolling saw on it. No table saw here at Slacker Boat Works.
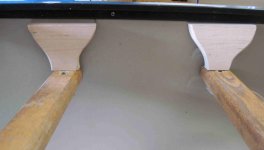
Trimmed and drilled. At Slacker Boat Works, we live with our mistakes. My first drilling attempt was done free hand with a slight angle applied to the shaft. That didn't work too well. The next 3 were drilled straight down using a drill press.
The error was larger than the photo shows. I drilled holes before trimming, so for that errant piece I trimmed the mistake end of the drop. The other three were trimmed on the gunwale face.
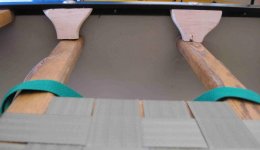
Spar urethane applied to all surfaces, pipe cleaner soaked in the spar urethane and slid thru the hole. 3 coats should be enough protection
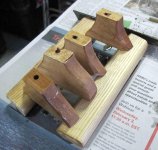
Thanks Mike!!
Some time ago, during a shop day with him he gifted me a clever little idea for a better seat drops than what you typically see on Old Town Canoes.
Having to hang around today for a repair man to show up and do some work for me seemed a perfect time to tackle this little project.
Here's a photo of the standard drilled dowel drop on top of the replacement mini-truss drops. The new drops look like they will seriously help inhibit seat sway.
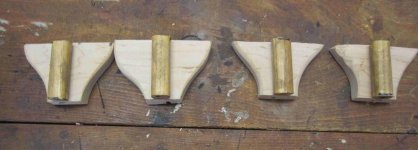
New drops laid in place. As crafted, they are a little too long for my preference. I like about 9.75 inches of seat clearance to more easily get my size 11s under the seat when I kneel. I'll need to take off 5cm to get the drop height I want. It took about 30 minutes of futzing around before I could figure out how to really secure the piece and get a electric scrolling saw on it. No table saw here at Slacker Boat Works.
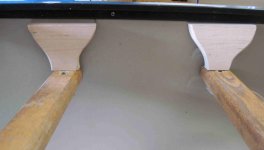
Trimmed and drilled. At Slacker Boat Works, we live with our mistakes. My first drilling attempt was done free hand with a slight angle applied to the shaft. That didn't work too well. The next 3 were drilled straight down using a drill press.
The error was larger than the photo shows. I drilled holes before trimming, so for that errant piece I trimmed the mistake end of the drop. The other three were trimmed on the gunwale face.
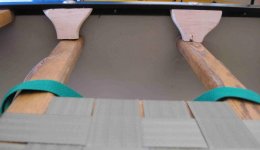
Spar urethane applied to all surfaces, pipe cleaner soaked in the spar urethane and slid thru the hole. 3 coats should be enough protection
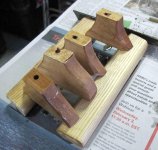
Thanks Mike!!