- Joined
- Jan 16, 2017
- Messages
- 42
- Reaction score
- 11
Greetings! I am new to the forum, but I have been lurking for some time.
I work for a company that produces both plastics and fiberglass products. In composites, we produce parts using the light RTM, vacuum bagging, chop, and wet layup processes. So, I have some experience with composites.
In his company dealings, my boss acquired an old company that has been producing fiberglass parts since the 1960s. In the warehouse of this old factory, there was and old composite canoe mold that was in fairly good shape for its age. My best guess is the mold is 30-40 years old.
Knowing that I like to canoe in the BWCA, my boss told me that I was welcome to refurbish the mold and build a canoe using leftover materials from the many R&D projects we have done over the years. I know....pretty sweet, right?
I have a few rolls of 5oz Kevlar, as well as fiberglass in various weights and weaves. I am trying to decide what would be the best laminate schedule with the epoxy resin I plan to use. I have also been toying with infusing the gunwales at the same time as I infuse the hull.
The mold will make a canoe that is about 18' long, with a 36" beam, and 12" height in the middle. It has three ribs in the bottom, with the center running from bow to stern acting as a keel. The stems are curved, hence the need to split the mold at the midpoint.
My goal is to mold a canoe that will weigh less than 60lbs all trimmed out. I hope to take it to the BWCA this year with my 16 year old son.
Does anyone recognize this design? My hunch is that this mold was created from a male plug, or a real canoe.
This should be a fun little project!
Here is the mold before the new orange surface coat. The original gelcoat was cracked and chipped.
IMG_2648 by bctc95, on Flickr
IMG_2649 by bctc95, on Flickr
IMG_2696 by bctc95, on Flickr
IMG_2697 by bctc95, on Flickr
IMG_2712 by bctc95, on Flickr
And after the new orange gelcoat.....
IMG_2713 by bctc95, on Flickr
IMG_2714 by bctc95, on Flickr
IMG_2715 by bctc95, on Flickr
Once I get the mold sanded and polished, it will be time to make a canoe.
I work for a company that produces both plastics and fiberglass products. In composites, we produce parts using the light RTM, vacuum bagging, chop, and wet layup processes. So, I have some experience with composites.
In his company dealings, my boss acquired an old company that has been producing fiberglass parts since the 1960s. In the warehouse of this old factory, there was and old composite canoe mold that was in fairly good shape for its age. My best guess is the mold is 30-40 years old.
Knowing that I like to canoe in the BWCA, my boss told me that I was welcome to refurbish the mold and build a canoe using leftover materials from the many R&D projects we have done over the years. I know....pretty sweet, right?
I have a few rolls of 5oz Kevlar, as well as fiberglass in various weights and weaves. I am trying to decide what would be the best laminate schedule with the epoxy resin I plan to use. I have also been toying with infusing the gunwales at the same time as I infuse the hull.
The mold will make a canoe that is about 18' long, with a 36" beam, and 12" height in the middle. It has three ribs in the bottom, with the center running from bow to stern acting as a keel. The stems are curved, hence the need to split the mold at the midpoint.
My goal is to mold a canoe that will weigh less than 60lbs all trimmed out. I hope to take it to the BWCA this year with my 16 year old son.
Does anyone recognize this design? My hunch is that this mold was created from a male plug, or a real canoe.
This should be a fun little project!
Here is the mold before the new orange surface coat. The original gelcoat was cracked and chipped.
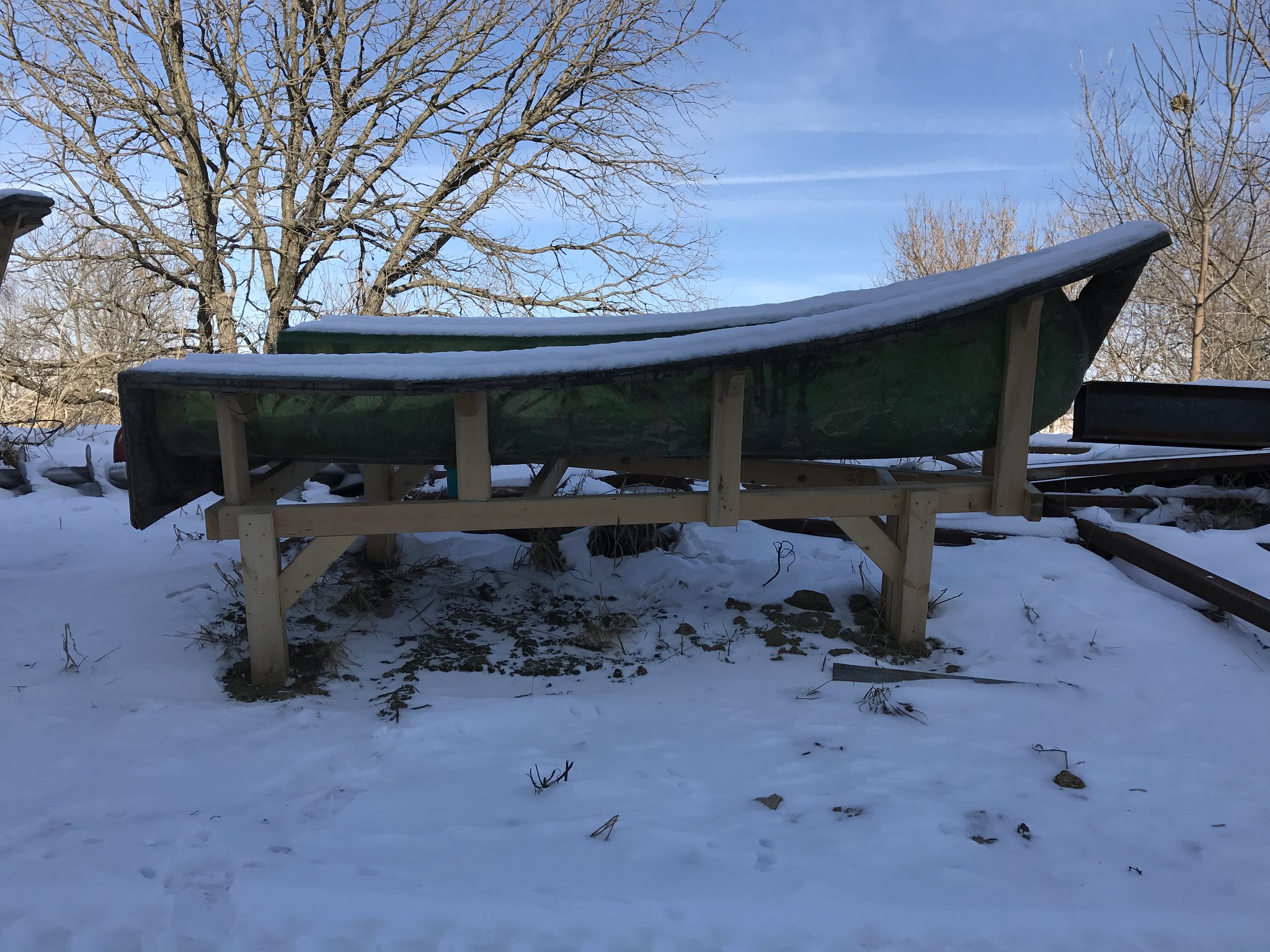
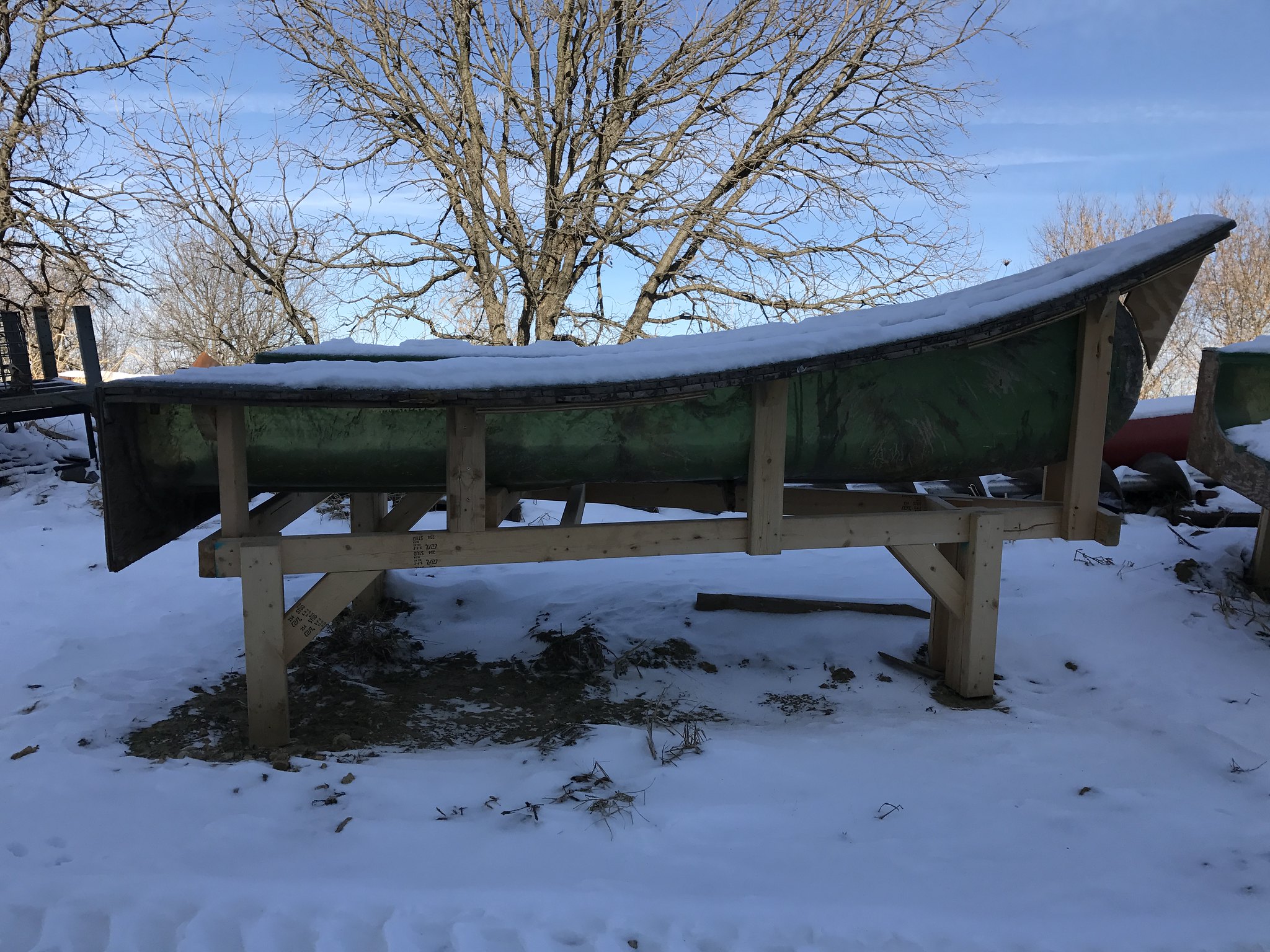
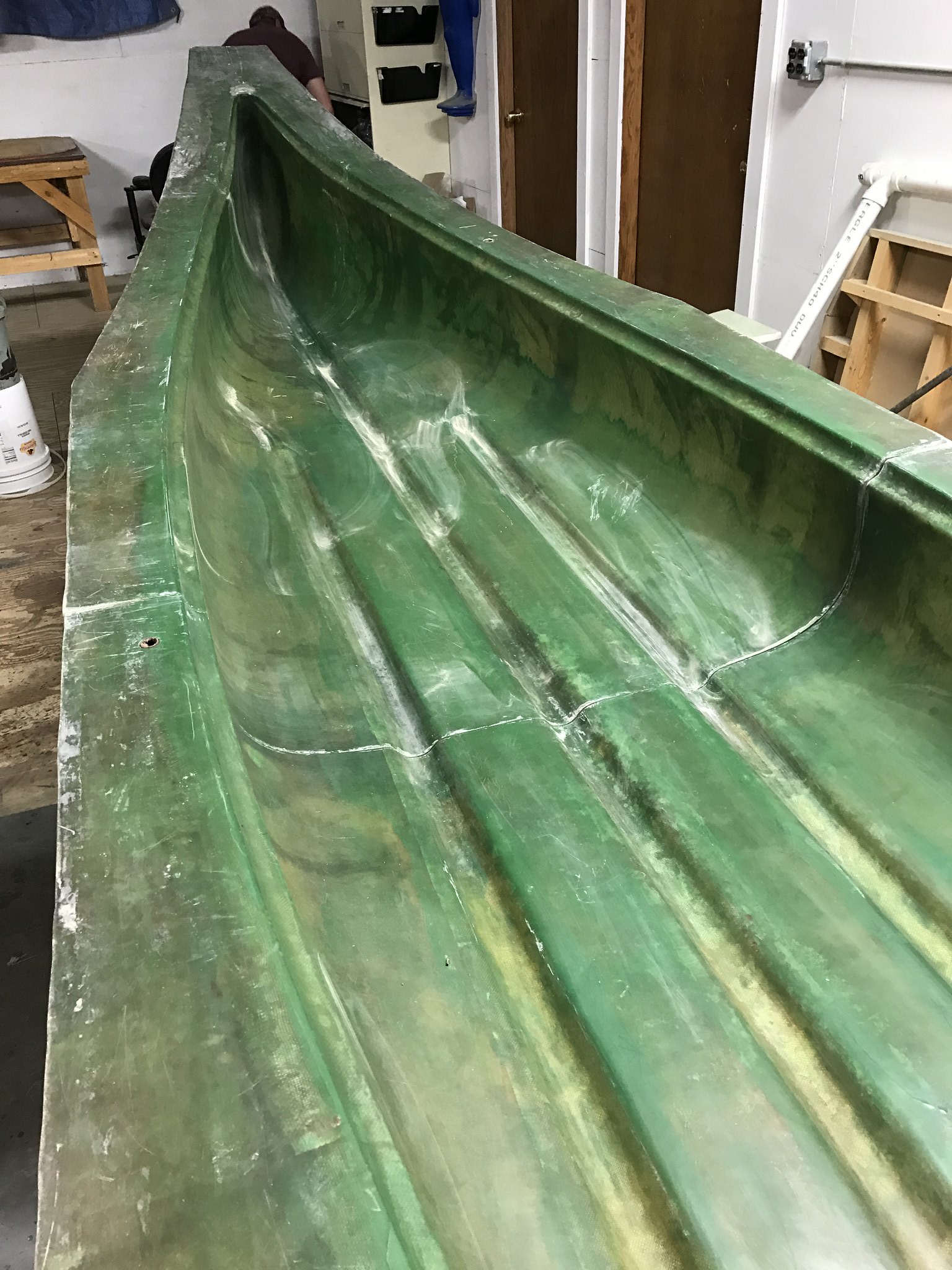
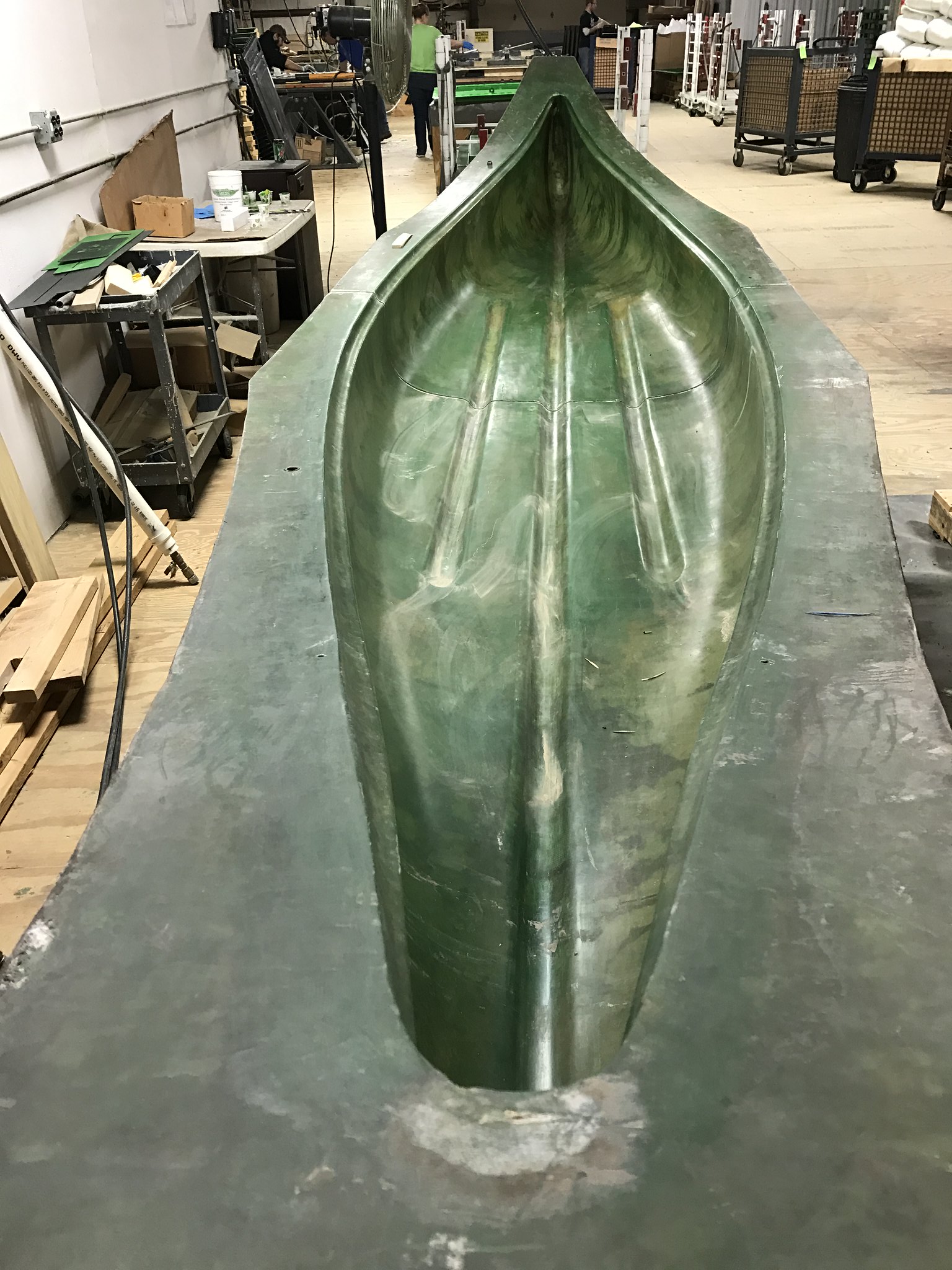
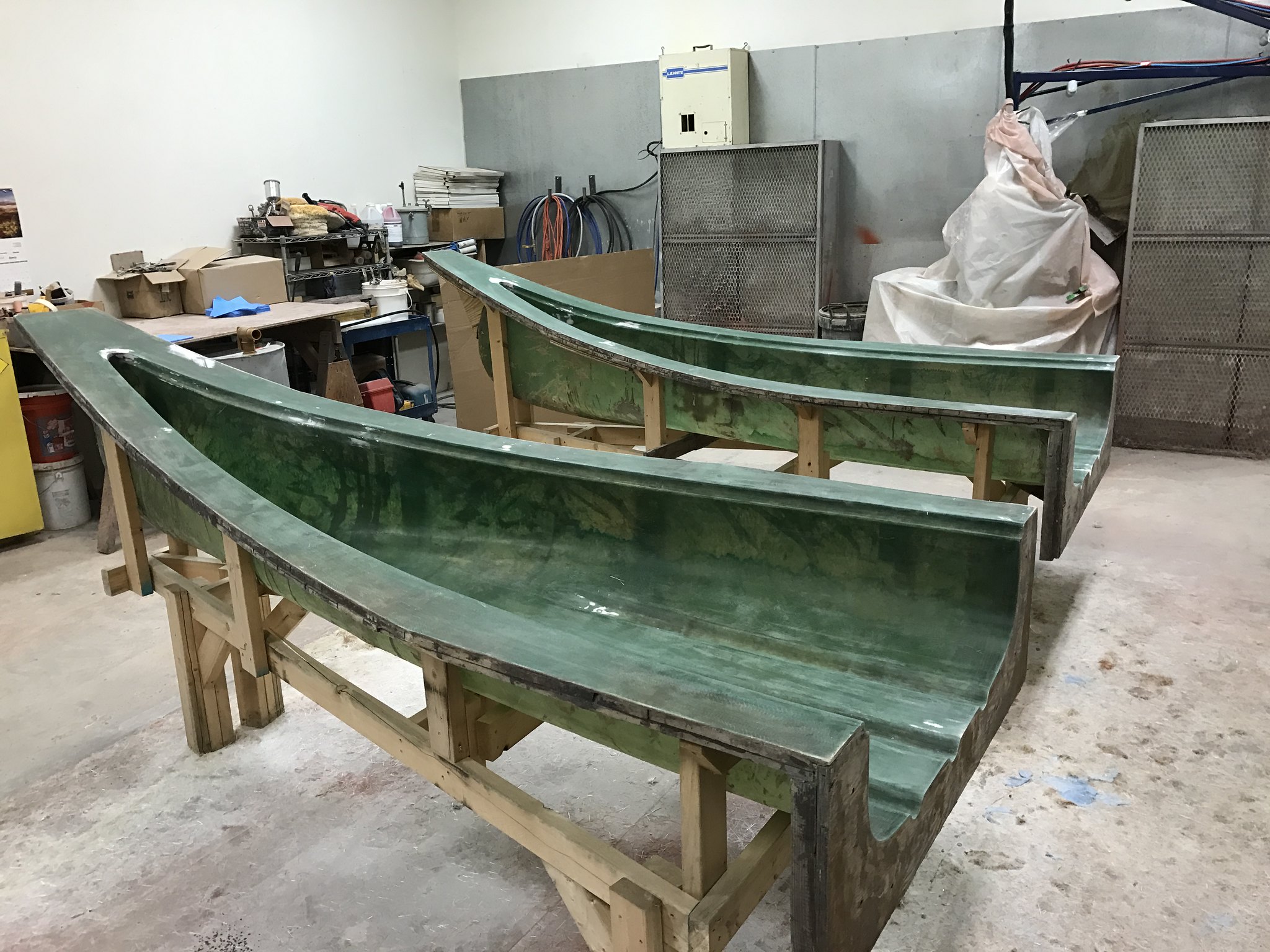
And after the new orange gelcoat.....
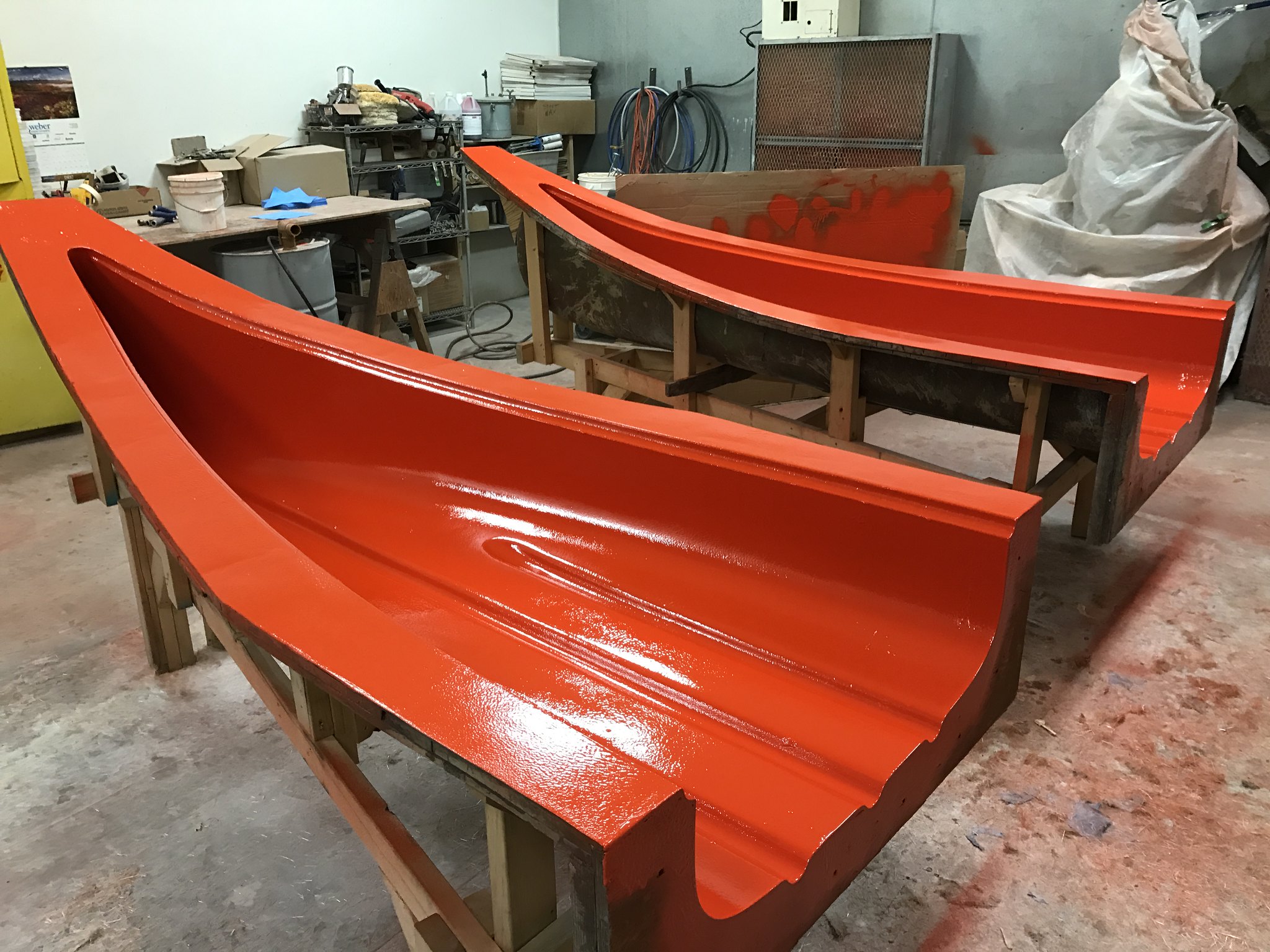
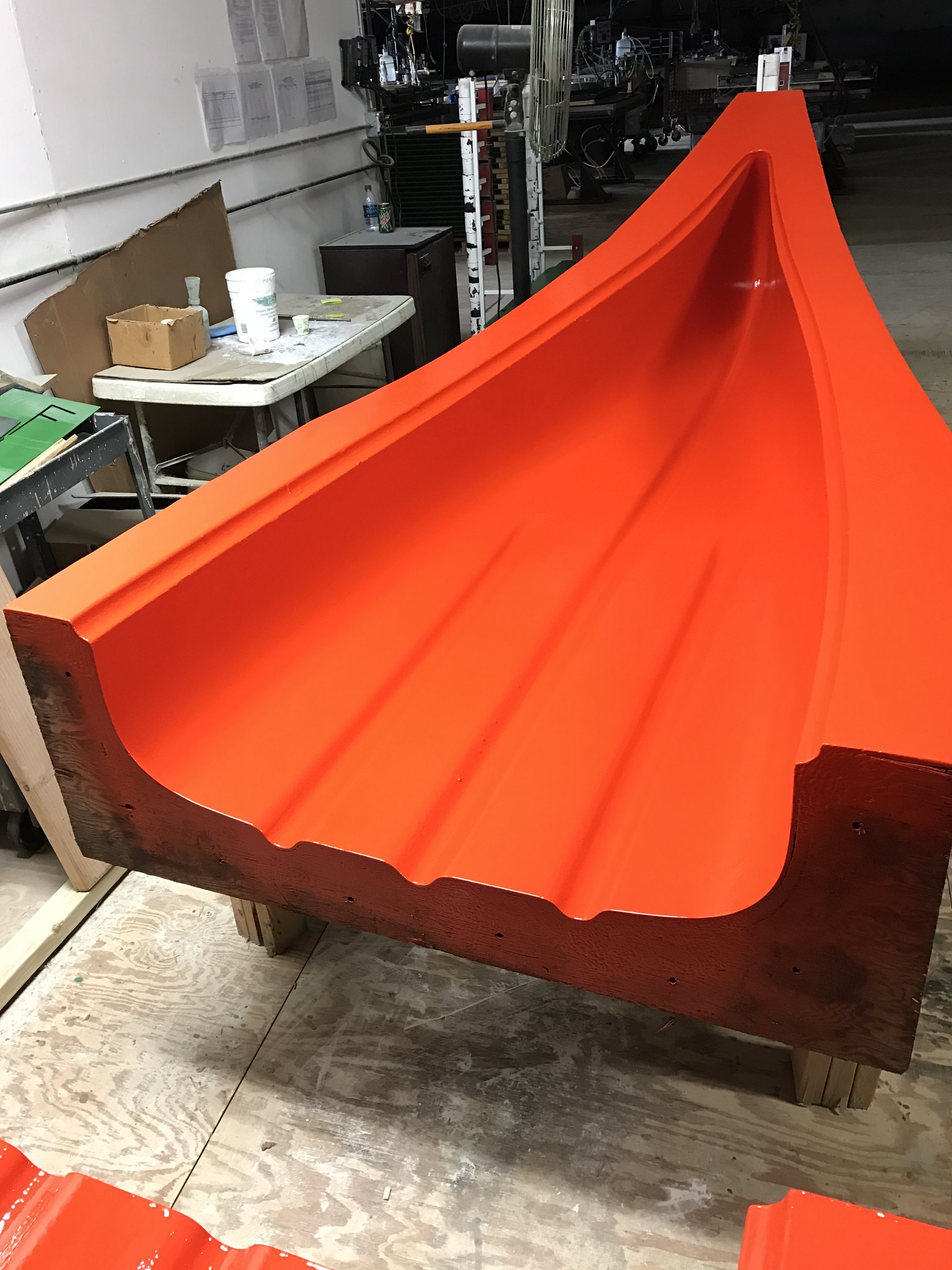
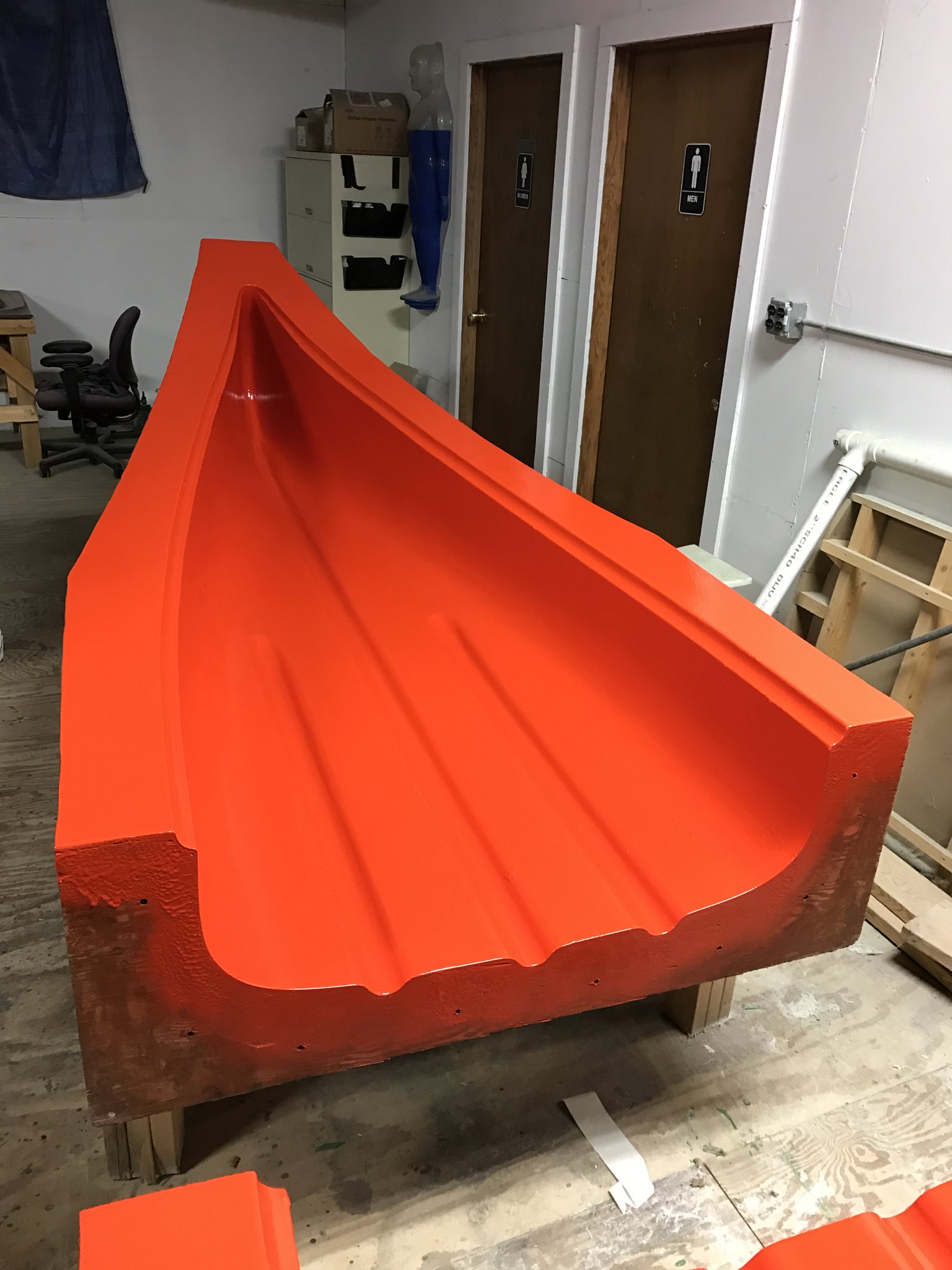
Once I get the mold sanded and polished, it will be time to make a canoe.
Attachments
Last edited: