Also: Another mystery project for you all.
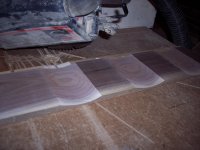
Anyone care to guess where this is going?
This technique is best done using a Radial Arm Saw. Looks something like this:
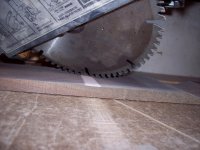
The blade is pulled out, lowered until it will just take a bite out of the wood, and pushed back. Raised just enough to clear the surface, and the process is repeated until you reach the depth you are after. The angle of the blade could be calculated, but it's simpler and faster to experiment on scrap.
I normally figure that safety is the user's business, but just in case anyone is tempted to try this out for their projects, I feel like I need to say the following:
- Clamps for the workpiece are not optional - this saw could throw the entire board across the room without half trying, and the loads on the blade are at unusual angles. Your normal tool sense does not operate in this zone.
- The rotation of the blade is always into the cut. No climb cuts here! They could blow up the blade.
If you do these two things, this operation is safer than many things people do regularly with a table saw or miter saw.
If you do not have access to a Radial Arm Saw, a tablesaw can be used. It takes some sturdy, precise jigs to make it reasonably safe, especially for crosscuts. Please do some research. The little direct drive 'mini' tablesaws have, I've heard, had issues with this sort of thing. People have seized up their drive bearings. The tables are not really large enough to support this, either.
If you do not have a tablesaw, either, Please seek the assistance of someone who does, or look into another method. The thought of someone attempting this with a skilsaw makes me cringe. If I seem to be panicking about this, please check Steve In Idaho's recent thread here in the construction forum: http://www.canoetripping.net/forums...3192-i-think-i-ll-just-put-this-here-gruesome
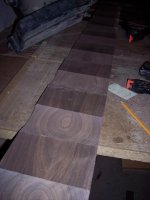
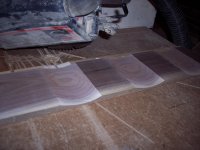
Anyone care to guess where this is going?
This technique is best done using a Radial Arm Saw. Looks something like this:
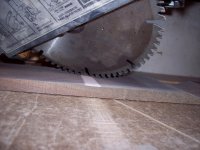
The blade is pulled out, lowered until it will just take a bite out of the wood, and pushed back. Raised just enough to clear the surface, and the process is repeated until you reach the depth you are after. The angle of the blade could be calculated, but it's simpler and faster to experiment on scrap.
I normally figure that safety is the user's business, but just in case anyone is tempted to try this out for their projects, I feel like I need to say the following:
- Clamps for the workpiece are not optional - this saw could throw the entire board across the room without half trying, and the loads on the blade are at unusual angles. Your normal tool sense does not operate in this zone.
- The rotation of the blade is always into the cut. No climb cuts here! They could blow up the blade.
If you do these two things, this operation is safer than many things people do regularly with a table saw or miter saw.
If you do not have access to a Radial Arm Saw, a tablesaw can be used. It takes some sturdy, precise jigs to make it reasonably safe, especially for crosscuts. Please do some research. The little direct drive 'mini' tablesaws have, I've heard, had issues with this sort of thing. People have seized up their drive bearings. The tables are not really large enough to support this, either.
If you do not have a tablesaw, either, Please seek the assistance of someone who does, or look into another method. The thought of someone attempting this with a skilsaw makes me cringe. If I seem to be panicking about this, please check Steve In Idaho's recent thread here in the construction forum: http://www.canoetripping.net/forums...3192-i-think-i-ll-just-put-this-here-gruesome