Here's a couple of pics, that I hope will illustrate better what I'm saying !
Note the lines on the leading edge of the stem forms. When tapering the forms, these lines, (layers of plys) make a reference point, so you can compare left to right.
Another thing I do is I lower my stem forms an 1/8-1/4" On my earlier builds I would always have a high spot on my hull at the stems. To help correct that I lowered my stem forms a little.
On this set, the stem form is a little too low, but didn't cause any trouble.
Again, I hope this helps !
Jim
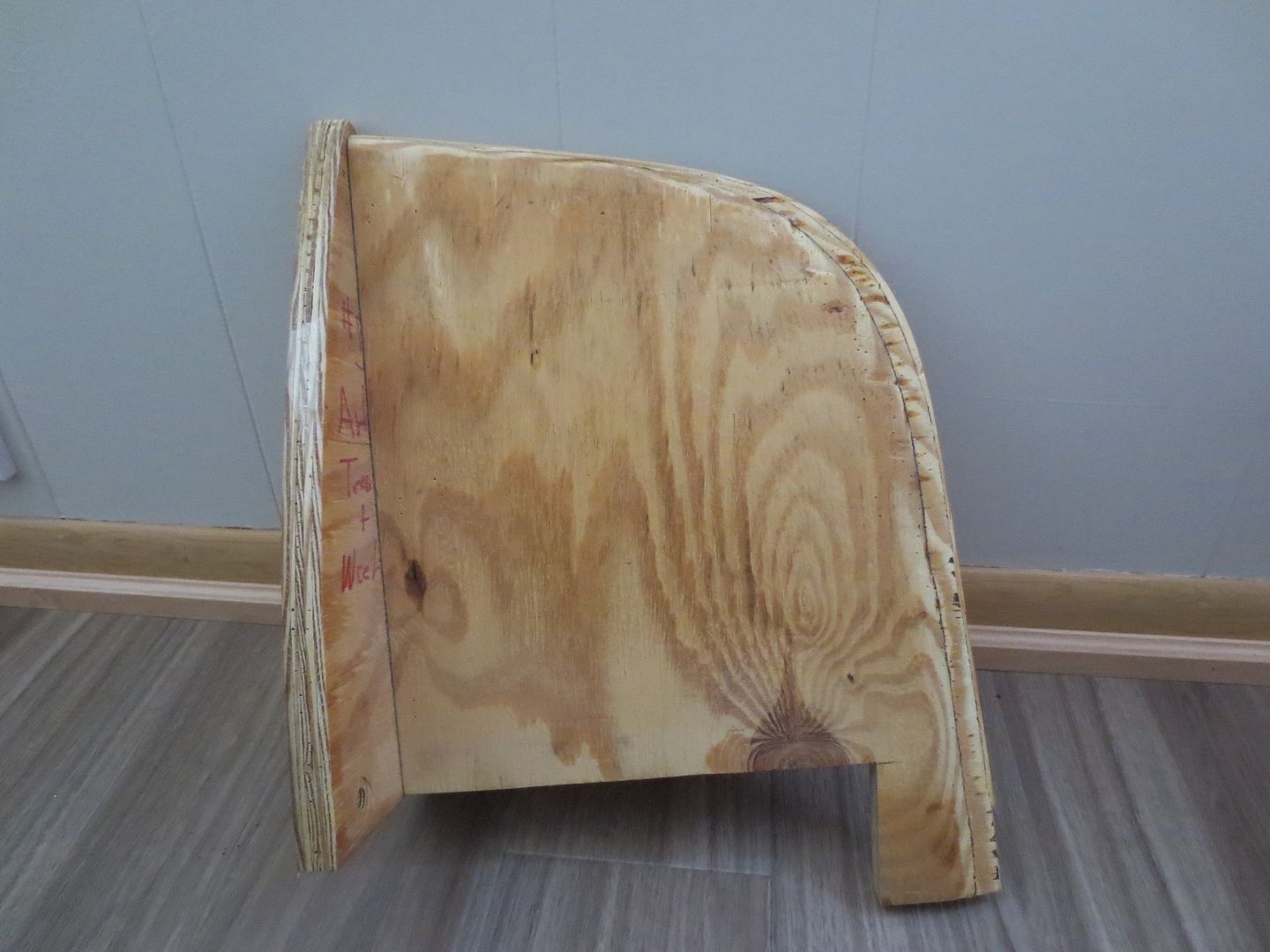
Note the lines on the leading edge of the stem forms. When tapering the forms, these lines, (layers of plys) make a reference point, so you can compare left to right.
Another thing I do is I lower my stem forms an 1/8-1/4" On my earlier builds I would always have a high spot on my hull at the stems. To help correct that I lowered my stem forms a little.
On this set, the stem form is a little too low, but didn't cause any trouble.
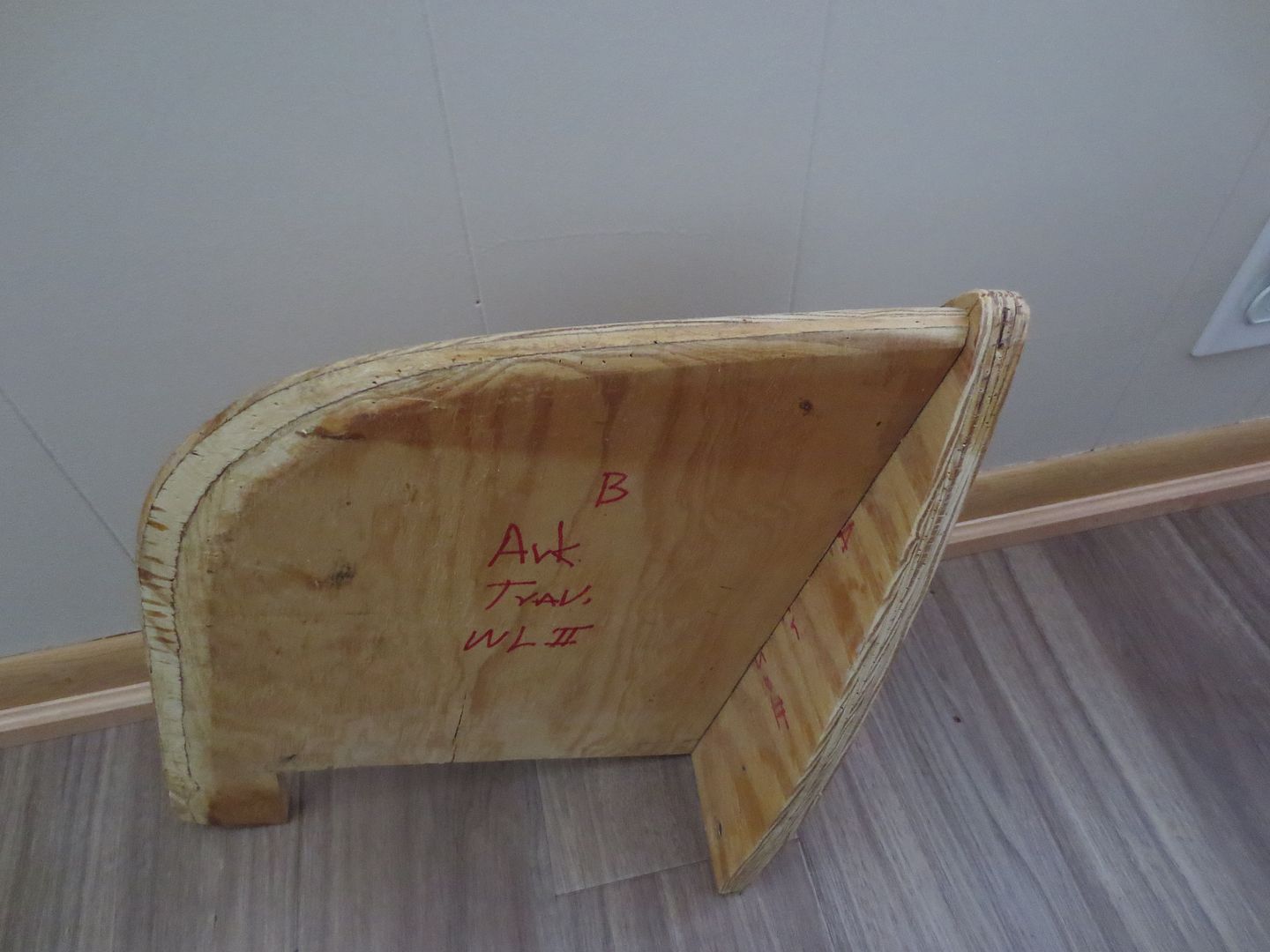
Again, I hope this helps !
Jim