OK seems a few people have been into various tests. And It's about time I come up with one.
This Summer, if all goes well, I'm going to attempt my second Kevlar canoe.
I will be using the stripper, that I'm building now as the male mold.
Years ago I purchased 9oz Stitched Kevlar from RAKA.It must have been designed for bullet proof vests, as I had a MOST difficult time cutting this Kevlar. It was also quite difficult to wet out. At that time I was using System Three's Clear Coat, which normally wets out E-glass quite easily.
As RAKA didn't have this in stock, lately. I ordered 8.9oz 2x2Kevlar twill from Noah. I cut a small piece to see how it compared to the RAKA 9oz stitched.
Noahs 8.9oz cut much easier, and wet out much easier.
Tomorrow I'll check on the pieces that I wet out, as far as stiffness, and cut ability.
As of right now, I'm really liking the Noah's 8.9 Kevlar.
If anyone has some Kevlar experience to share, Please post !!!!
RAKA 9oz Stitched on the left, Noah's 8.9oz 2x2 Kevlar Twill, on the right.
Jim
This Summer, if all goes well, I'm going to attempt my second Kevlar canoe.
I will be using the stripper, that I'm building now as the male mold.
Years ago I purchased 9oz Stitched Kevlar from RAKA.It must have been designed for bullet proof vests, as I had a MOST difficult time cutting this Kevlar. It was also quite difficult to wet out. At that time I was using System Three's Clear Coat, which normally wets out E-glass quite easily.
As RAKA didn't have this in stock, lately. I ordered 8.9oz 2x2Kevlar twill from Noah. I cut a small piece to see how it compared to the RAKA 9oz stitched.
Noahs 8.9oz cut much easier, and wet out much easier.
Tomorrow I'll check on the pieces that I wet out, as far as stiffness, and cut ability.
As of right now, I'm really liking the Noah's 8.9 Kevlar.
If anyone has some Kevlar experience to share, Please post !!!!
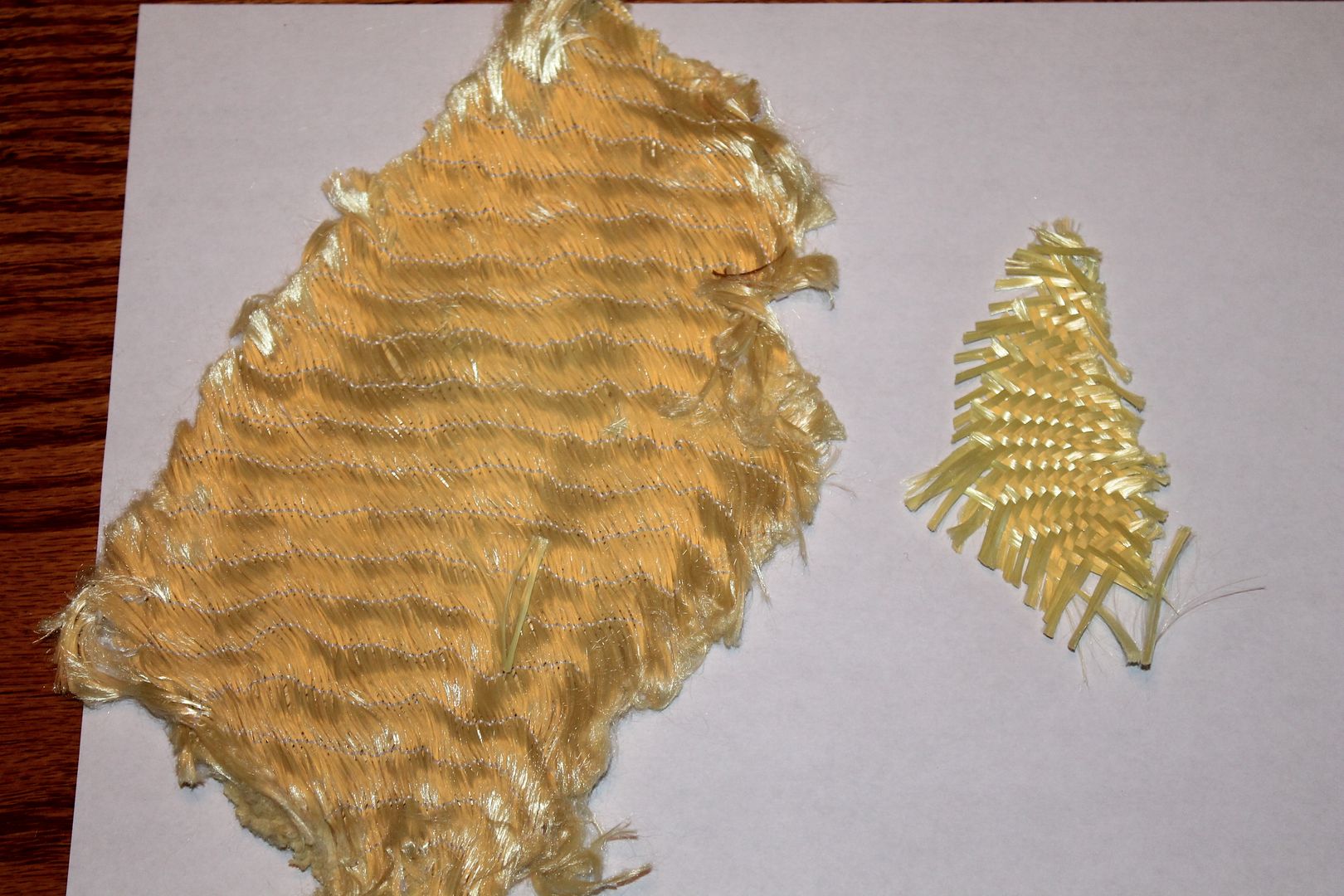
RAKA 9oz Stitched on the left, Noah's 8.9oz 2x2 Kevlar Twill, on the right.
Jim
Last edited: