Well that makes me feel better. I have this French curve looking scraper that in using in the chine area, seems to be working ok. After scraping I'll quickly hand sand and say good enough. Good observation on the forms, they are a pain in the neck.
Mem kayak folks always drill through the hull for lifting handles. Just fit a block of wood and epoxy in place first before drilling the hole. Then follow up with epoxy to seal it. I guess I'll do it. I hope the drill doesn't grab and rip my hull in half!
It took me quite a long time to develop the courage to drill through my hull. I actually thought that it was the least of the two evils between drilling through the deck and the hull. I'm strange like that

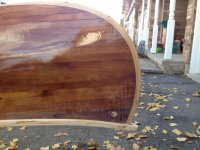