This would be of most interest to anyone thinking about building a fuselage frame style skin on frame canoe or other paddle craft, but I think there might be some general utility for anyone either building or repairing other styles of boats as well. It’s a pretty crude approach to stress testing, and the material sizes here are pretty specific, but it’s all I got - take it for what it is worth.
Basically, for my project I wanted to find out what combination of wood with fibreglass or carbon fibre laminations would get me more or less equivalent strength, at less weight, than some selected baseline, wood only scantlings. I was not looking to determine the absolute strength of any test pieces, but only their relative strength within the confines of the primitive testing mechanisms I was able to put together - e.g. if subject to the same stress, would a .5 x .75 piece of carbon-sleeve wrapped cedar be as strong but weigh significantly less than a “baseline” .75 x .75 piece of bare cedar?
My test subjects were 1/8 and 1/4 inch thick Baltic Birch plywood relative to 3/8 inch thick Baltic Birch, and .5x.5 and .5x.75 inch cedar relative to .75x.75 cedar. I used 6 ounce fibreglass and carbon fibre cloth, and 8.9 ounce carbon sleeve, as noted in the table below. For curiosity sake I also tried a very limited test of of Corecell A500 foam, and some 4 ounce s glass (which I just realized has some wonky results on the table which I think is a data entry error of some kind), also as noted.
For the plywood pieces, I used a gym weight tree with one end positioned on the plywood as it was suspended across a pair of dumbbells, and just added weights to the tree in 2.5 pound increments until the piece broke. The weight tree weights 22 pounds, but because one end is resting on the ground the “baseline” weight actually applied to the test piece was only 12 pounds before adding any additional weights.
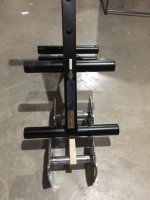
For the cedar scantlings, in order to let me add the necessary weight I had to suspend the weight tree from the test pieces, with the whole thing hanging about 6 inches from the floor, and added weights accordingly (again in 2.5 pound increments). Baseline weight here is the full 22 pounds of the weight tree.
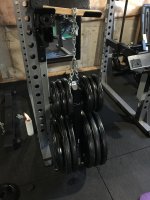
All laminations were done by hand in a wet layup - for the plywood I used peel ply and paper towels under wax paper to absorb excess epoxy while pressed between two boards under 80 pounds of weights until cured. For the carbon sleeve I used a gloved hand to compress and “squeegee” the sleeve once epoxied, and then just left hanging to cure. All pieces were cured at least 72 hours at about 65-70 degrees F before testing.
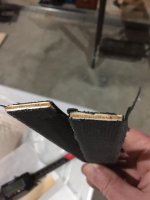
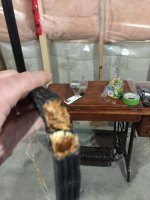
The data are below. As this post is getting a bit long I won’t get into any detail. There are a few combinations that have some potential, but the upshot for me is that for any combination with strength approaching the baseline, the weight savings are pretty small or non-existent. Within the wood sizes and budget I am looking at here, it just doesn’t seem worth it to go through the trouble and cost of laminations for the marginal weight savings over baseline I would get. Given the importance of core thickness and length for lamination strength, I think it might be a different story with beefier pieces. I will be looking at this when I start on seats, thwarts, etc for my canoe build, but in the meantime if there are any comments or observations on this set of tests ....
thanks all
Tony
[TABLE="cellpadding: 0, cellspacing: 0"]
[TR]
[TD] [/TD]
[TD] [/TD]
[TD] [/TD]
[TD] [/TD]
[TD] [/TD]
[TD] [/TD]
[TD] [/TD]
[TD] [/TD]
[TD] [/TD]
[/TR]
[TR]
[TD] [/TD]
[TD="colspan: 4"]Wood core and laminate stress tests[/TD]
[TD] [/TD]
[TD] [/TD]
[TD] [/TD]
[TD] [/TD]
[/TR]
[TR]
[TD] [/TD]
[TD] [/TD]
[TD] [/TD]
[TD] [/TD]
[TD] [/TD]
[/TR]
[TR]
[TD] [/TD]
[TD]Weight (grams)[/TD]
[TD]Base pounds of testing device[/TD]
[TD]Additional pounds[/TD]
[TD]Total pounds to failure[/TD]
[TD]Total pounds to failure relative to baseline[/TD]
[TD]Weight relative to baseline[/TD]
[TD] [/TD]
[TD] [/TD]
[/TR]
[TR]
[TD]Plywood Stress Test *[/TD]
[TD] [/TD]
[TD] [/TD]
[TD] [/TD]
[TD] [/TD]
[TD] [/TD]
[TD] [/TD]
[TD] [/TD]
[TD] [/TD]
[/TR]
[TR]
[TD] [/TD]
[TD] [/TD]
[TD] [/TD]
[TD] [/TD]
[TD] [/TD]
[TD] [/TD]
[TD] [/TD]
[TD] [/TD]
[TD] [/TD]
[/TR]
[TR]
[TD]Baseline - 3/8 Baltic Birch, plain[/TD]
[TD]42[/TD]
[TD]12.0[/TD]
[TD]122.5[/TD]
[TD]134.5[/TD]
[TD]100.0%[/TD]
[TD]100.0%[/TD]
[TD] [/TD]
[TD] [/TD]
[/TR]
[TR]
[TD] [/TD]
[TD] [/TD]
[TD] [/TD]
[TD] [/TD]
[TD] [/TD]
[TD] [/TD]
[TD] [/TD]
[TD] [/TD]
[TD] [/TD]
[/TR]
[TR]
[TD]Samples[/TD]
[TD] [/TD]
[TD] [/TD]
[TD] [/TD]
[TD] [/TD]
[TD] [/TD]
[TD] [/TD]
[TD] [/TD]
[TD] [/TD]
[/TR]
[TR]
[TD]1/8 plain[/TD]
[TD]15[/TD]
[TD]12.0[/TD]
[TD]0.0[/TD]
[TD]12.0[/TD]
[TD]8.9%[/TD]
[TD]35.7%[/TD]
[TD] [/TD]
[TD] [/TD]
[/TR]
[TR]
[TD]1/8 1 layer e glass[/TD]
[TD]22[/TD]
[TD]12.0[/TD]
[TD]15.0[/TD]
[TD]27.0[/TD]
[TD]20.1%[/TD]
[TD]52.4%[/TD]
[TD] [/TD]
[TD] [/TD]
[/TR]
[TR]
[TD]1/8 2 layers e glass[/TD]
[TD]26[/TD]
[TD]12.0[/TD]
[TD]20.0[/TD]
[TD]32.0[/TD]
[TD]23.8%[/TD]
[TD]61.9%[/TD]
[TD] [/TD]
[TD] [/TD]
[/TR]
[TR]
[TD]1/8 1 layer carbon[/TD]
[TD]21[/TD]
[TD]12.0[/TD]
[TD]30.0[/TD]
[TD]42.0[/TD]
[TD]31.2%[/TD]
[TD]50.0%[/TD]
[TD] [/TD]
[TD] [/TD]
[/TR]
[TR]
[TD]1/8 1 layer carbon, 1 layer e glass[/TD]
[TD]29[/TD]
[TD]12.0[/TD]
[TD]55.0[/TD]
[TD]67.0[/TD]
[TD]49.8%[/TD]
[TD]69.0%[/TD]
[TD] [/TD]
[TD] [/TD]
[/TR]
[TR]
[TD]1/8 2 layer carbon[/TD]
[TD]27[/TD]
[TD]12.0[/TD]
[TD]70.0[/TD]
[TD]82.0[/TD]
[TD]61.0%[/TD]
[TD]64.3%[/TD]
[TD] [/TD]
[TD] [/TD]
[/TR]
[TR]
[TD] [/TD]
[TD] [/TD]
[TD] [/TD]
[TD] [/TD]
[TD] [/TD]
[TD] [/TD]
[TD] [/TD]
[TD] [/TD]
[TD] [/TD]
[/TR]
[TR]
[TD]1/4 plain[/TD]
[TD]28[/TD]
[TD]12.0[/TD]
[TD]57.5[/TD]
[TD]69.5[/TD]
[TD]51.7%[/TD]
[TD]66.7%[/TD]
[TD] [/TD]
[TD] [/TD]
[/TR]
[TR]
[TD]1/4 1 layer e glass[/TD]
[TD]34[/TD]
[TD]12.0[/TD]
[TD]75.0[/TD]
[TD]87.0[/TD]
[TD]64.7%[/TD]
[TD]81.0%[/TD]
[TD] [/TD]
[TD] [/TD]
[/TR]
[TR]
[TD]1/4 2 layers 4 ounce s glass[/TD]
[TD]35[/TD]
[TD]12.0[/TD]
[TD]50.0[/TD]
[TD]62.0[/TD]
[TD]46.1%[/TD]
[TD]83.3%[/TD]
[TD] [/TD]
[TD] [/TD]
[/TR]
[TR]
[TD]1/4 1 layer carbon[/TD]
[TD]36[/TD]
[TD]12.0[/TD]
[TD]107.5[/TD]
[TD]119.5[/TD]
[TD]88.8%[/TD]
[TD]85.7%[/TD]
[TD] [/TD]
[TD] [/TD]
[/TR]
[TR]
[TD]1/4 1 layer carbon, 1 layer e glass[/TD]
[TD]40[/TD]
[TD]12.0[/TD]
[TD]135.0[/TD]
[TD]147.0[/TD]
[TD]109.3%[/TD]
[TD]95.2%[/TD]
[TD] [/TD]
[TD] [/TD]
[/TR]
[TR]
[TD] [/TD]
[TD] [/TD]
[TD] [/TD]
[TD] [/TD]
[TD] [/TD]
[TD] [/TD]
[TD] [/TD]
[TD] [/TD]
[TD] [/TD]
[/TR]
[TR]
[TD] [/TD]
[TD] [/TD]
[TD] [/TD]
[TD] [/TD]
[TD] [/TD]
[TD] [/TD]
[TD] [/TD]
[TD] [/TD]
[TD] [/TD]
[/TR]
[TR]
[TD]Stringer Stress Test **[/TD]
[TD]Weight (grams)[/TD]
[TD]Base pounds of testing device[/TD]
[TD]Additional pounds[/TD]
[TD]Total pounds to failure[/TD]
[TD]Total pounds to failure relative to baseline[/TD]
[TD]Weight relative to baseline[/TD]
[TD] [/TD]
[TD] [/TD]
[/TR]
[TR]
[TD] [/TD]
[TD] [/TD]
[TD] [/TD]
[TD] [/TD]
[TD] [/TD]
[TD] [/TD]
[TD] [/TD]
[TD] [/TD]
[TD] [/TD]
[/TR]
[TR]
[TD]Baseline - 0.75 x 0.75 plain cedar[/TD]
[TD]48[/TD]
[TD]22.0[/TD]
[TD]390[/TD]
[TD]412.0[/TD]
[TD]100.0%[/TD]
[TD]100%[/TD]
[TD] [/TD]
[TD] [/TD]
[/TR]
[TR]
[TD] [/TD]
[TD] [/TD]
[TD] [/TD]
[TD] [/TD]
[TD] [/TD]
[TD] [/TD]
[TD] [/TD]
[TD] [/TD]
[TD] [/TD]
[/TR]
[TR]
[TD]Samples[/TD]
[TD] [/TD]
[TD] [/TD]
[TD] [/TD]
[TD] [/TD]
[TD] [/TD]
[TD] [/TD]
[TD] [/TD]
[TD] [/TD]
[/TR]
[TR]
[TD]0.5 x 0.5 plain cedar[/TD]
[TD]22[/TD]
[TD]22.0[/TD]
[TD]145[/TD]
[TD]167.0[/TD]
[TD]41.5%[/TD]
[TD]45.8%[/TD]
[TD] [/TD]
[TD] [/TD]
[/TR]
[TR]
[TD]0.5 x 0.5 cedar 2 layers of carbon sleeve[/TD]
[TD]43[/TD]
[TD]22.0[/TD]
[TD]250[/TD]
[TD]272.0[/TD]
[TD]67.7%[/TD]
[TD]89.6%[/TD]
[TD] [/TD]
[TD] [/TD]
[/TR]
[TR]
[TD]0.5 x 0.75 plain cedar[/TD]
[TD]32[/TD]
[TD]22.0[/TD]
[TD]215[/TD]
[TD]237.0[/TD]
[TD]59.0%[/TD]
[TD]66.7%[/TD]
[TD] [/TD]
[TD] [/TD]
[/TR]
[TR]
[TD]0.5 x 0.75 cedar 1 layer of carbon sleeve[/TD]
[TD]46[/TD]
[TD]22.0[/TD]
[TD]300[/TD]
[TD]322.0[/TD]
[TD]80.1%[/TD]
[TD]95.8%[/TD]
[TD] [/TD]
[TD] [/TD]
[/TR]
[TR]
[TD]0.5 x 0.6 Corecell A500 foam[/TD]
[TD]9[/TD]
[TD]22.0[/TD]
[TD] [/TD]
[TD]22.0[/TD]
[TD]5.5%[/TD]
[TD]18.8%[/TD]
[TD] [/TD]
[TD] [/TD]
[/TR]
[TR]
[TD]0.5 x 0.6 Corecell A500 2 layers of carbon sleeve[/TD]
[TD]33[/TD]
[TD]22.0[/TD]
[TD]75[/TD]
[TD]97.0[/TD]
[TD]24.1%[/TD]
[TD]68.8%[/TD]
[TD] [/TD]
[TD] [/TD]
[/TR]
[TR]
[TD] [/TD]
[TD] [/TD]
[TD] [/TD]
[TD] [/TD]
[TD] [/TD]
[TD] [/TD]
[TD] [/TD]
[TD] [/TD]
[TD] [/TD]
[/TR]
[TR]
[TD] [/TD]
[TD="colspan: 7"]* Baltic Birch (1/8 and 1/4 inch thickness, 1x10 inch samples) with selected carbon fibre and fibreglass laminations (6 ounce/sq. yd. carbon and e glass cloth, laminated top and bottom, with exception of one test of 4 ounce s glass as noted for 1/4 inch plywood ), test weight applied on mid point of flat face of samples, across 8 inch span[/TD]
[TD] [/TD]
[/TR]
[TR]
[TD] [/TD]
[TD="colspan: 7"]** Stringer stress test - 12 inch long samples using 8.9 ounce biaxial carbon fibre tubular sleeve (0.75” diameter) as indicated, test weight applied at mid point on edge of widest dimension, across 6 inch span[/TD]
[TD] [/TD]
[/TR]
[TR]
[TD] [/TD]
[TD="colspan: 7"] [/TD]
[TD] [/TD]
[/TR]
[TR]
[TD] [/TD]
[TD="colspan: 7"] [/TD]
[TD] [/TD]
[/TR]
[TR]
[TD] [/TD]
[TD="colspan: 7"] [/TD]
[TD] [/TD]
[/TR]
[TR]
[TD] [/TD]
[TD="colspan: 7"] [/TD]
[TD] [/TD]
[/TR]
[TR]
[TD] [/TD]
[TD="colspan: 7"] [/TD]
[TD] [/TD]
[/TR]
[TR]
[TD] [/TD]
[TD="colspan: 7"] [/TD]
[TD] [/TD]
[/TR]
[TR]
[TD] [/TD]
[TD="colspan: 7"] [/TD]
[TD] [/TD]
[/TR]
[TR]
[TD] [/TD]
[TD="colspan: 7"] [/TD]
[TD] [/TD]
[/TR]
[TR]
[TD] [/TD]
[TD="colspan: 7"] [/TD]
[TD] [/TD]
[/TR]
[/TABLE]
Basically, for my project I wanted to find out what combination of wood with fibreglass or carbon fibre laminations would get me more or less equivalent strength, at less weight, than some selected baseline, wood only scantlings. I was not looking to determine the absolute strength of any test pieces, but only their relative strength within the confines of the primitive testing mechanisms I was able to put together - e.g. if subject to the same stress, would a .5 x .75 piece of carbon-sleeve wrapped cedar be as strong but weigh significantly less than a “baseline” .75 x .75 piece of bare cedar?
My test subjects were 1/8 and 1/4 inch thick Baltic Birch plywood relative to 3/8 inch thick Baltic Birch, and .5x.5 and .5x.75 inch cedar relative to .75x.75 cedar. I used 6 ounce fibreglass and carbon fibre cloth, and 8.9 ounce carbon sleeve, as noted in the table below. For curiosity sake I also tried a very limited test of of Corecell A500 foam, and some 4 ounce s glass (which I just realized has some wonky results on the table which I think is a data entry error of some kind), also as noted.
For the plywood pieces, I used a gym weight tree with one end positioned on the plywood as it was suspended across a pair of dumbbells, and just added weights to the tree in 2.5 pound increments until the piece broke. The weight tree weights 22 pounds, but because one end is resting on the ground the “baseline” weight actually applied to the test piece was only 12 pounds before adding any additional weights.
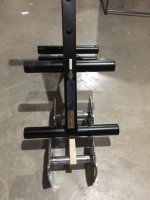
For the cedar scantlings, in order to let me add the necessary weight I had to suspend the weight tree from the test pieces, with the whole thing hanging about 6 inches from the floor, and added weights accordingly (again in 2.5 pound increments). Baseline weight here is the full 22 pounds of the weight tree.
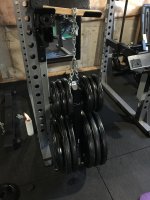
All laminations were done by hand in a wet layup - for the plywood I used peel ply and paper towels under wax paper to absorb excess epoxy while pressed between two boards under 80 pounds of weights until cured. For the carbon sleeve I used a gloved hand to compress and “squeegee” the sleeve once epoxied, and then just left hanging to cure. All pieces were cured at least 72 hours at about 65-70 degrees F before testing.
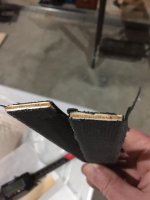
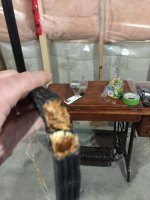
The data are below. As this post is getting a bit long I won’t get into any detail. There are a few combinations that have some potential, but the upshot for me is that for any combination with strength approaching the baseline, the weight savings are pretty small or non-existent. Within the wood sizes and budget I am looking at here, it just doesn’t seem worth it to go through the trouble and cost of laminations for the marginal weight savings over baseline I would get. Given the importance of core thickness and length for lamination strength, I think it might be a different story with beefier pieces. I will be looking at this when I start on seats, thwarts, etc for my canoe build, but in the meantime if there are any comments or observations on this set of tests ....
thanks all
Tony
[TABLE="cellpadding: 0, cellspacing: 0"]
[TR]
[TD] [/TD]
[TD] [/TD]
[TD] [/TD]
[TD] [/TD]
[TD] [/TD]
[TD] [/TD]
[TD] [/TD]
[TD] [/TD]
[TD] [/TD]
[/TR]
[TR]
[TD] [/TD]
[TD="colspan: 4"]Wood core and laminate stress tests[/TD]
[TD] [/TD]
[TD] [/TD]
[TD] [/TD]
[TD] [/TD]
[/TR]
[TR]
[TD] [/TD]
[TD] [/TD]
[TD] [/TD]
[TD] [/TD]
[TD] [/TD]
[/TR]
[TR]
[TD] [/TD]
[TD]Weight (grams)[/TD]
[TD]Base pounds of testing device[/TD]
[TD]Additional pounds[/TD]
[TD]Total pounds to failure[/TD]
[TD]Total pounds to failure relative to baseline[/TD]
[TD]Weight relative to baseline[/TD]
[TD] [/TD]
[TD] [/TD]
[/TR]
[TR]
[TD]Plywood Stress Test *[/TD]
[TD] [/TD]
[TD] [/TD]
[TD] [/TD]
[TD] [/TD]
[TD] [/TD]
[TD] [/TD]
[TD] [/TD]
[TD] [/TD]
[/TR]
[TR]
[TD] [/TD]
[TD] [/TD]
[TD] [/TD]
[TD] [/TD]
[TD] [/TD]
[TD] [/TD]
[TD] [/TD]
[TD] [/TD]
[TD] [/TD]
[/TR]
[TR]
[TD]Baseline - 3/8 Baltic Birch, plain[/TD]
[TD]42[/TD]
[TD]12.0[/TD]
[TD]122.5[/TD]
[TD]134.5[/TD]
[TD]100.0%[/TD]
[TD]100.0%[/TD]
[TD] [/TD]
[TD] [/TD]
[/TR]
[TR]
[TD] [/TD]
[TD] [/TD]
[TD] [/TD]
[TD] [/TD]
[TD] [/TD]
[TD] [/TD]
[TD] [/TD]
[TD] [/TD]
[TD] [/TD]
[/TR]
[TR]
[TD]Samples[/TD]
[TD] [/TD]
[TD] [/TD]
[TD] [/TD]
[TD] [/TD]
[TD] [/TD]
[TD] [/TD]
[TD] [/TD]
[TD] [/TD]
[/TR]
[TR]
[TD]1/8 plain[/TD]
[TD]15[/TD]
[TD]12.0[/TD]
[TD]0.0[/TD]
[TD]12.0[/TD]
[TD]8.9%[/TD]
[TD]35.7%[/TD]
[TD] [/TD]
[TD] [/TD]
[/TR]
[TR]
[TD]1/8 1 layer e glass[/TD]
[TD]22[/TD]
[TD]12.0[/TD]
[TD]15.0[/TD]
[TD]27.0[/TD]
[TD]20.1%[/TD]
[TD]52.4%[/TD]
[TD] [/TD]
[TD] [/TD]
[/TR]
[TR]
[TD]1/8 2 layers e glass[/TD]
[TD]26[/TD]
[TD]12.0[/TD]
[TD]20.0[/TD]
[TD]32.0[/TD]
[TD]23.8%[/TD]
[TD]61.9%[/TD]
[TD] [/TD]
[TD] [/TD]
[/TR]
[TR]
[TD]1/8 1 layer carbon[/TD]
[TD]21[/TD]
[TD]12.0[/TD]
[TD]30.0[/TD]
[TD]42.0[/TD]
[TD]31.2%[/TD]
[TD]50.0%[/TD]
[TD] [/TD]
[TD] [/TD]
[/TR]
[TR]
[TD]1/8 1 layer carbon, 1 layer e glass[/TD]
[TD]29[/TD]
[TD]12.0[/TD]
[TD]55.0[/TD]
[TD]67.0[/TD]
[TD]49.8%[/TD]
[TD]69.0%[/TD]
[TD] [/TD]
[TD] [/TD]
[/TR]
[TR]
[TD]1/8 2 layer carbon[/TD]
[TD]27[/TD]
[TD]12.0[/TD]
[TD]70.0[/TD]
[TD]82.0[/TD]
[TD]61.0%[/TD]
[TD]64.3%[/TD]
[TD] [/TD]
[TD] [/TD]
[/TR]
[TR]
[TD] [/TD]
[TD] [/TD]
[TD] [/TD]
[TD] [/TD]
[TD] [/TD]
[TD] [/TD]
[TD] [/TD]
[TD] [/TD]
[TD] [/TD]
[/TR]
[TR]
[TD]1/4 plain[/TD]
[TD]28[/TD]
[TD]12.0[/TD]
[TD]57.5[/TD]
[TD]69.5[/TD]
[TD]51.7%[/TD]
[TD]66.7%[/TD]
[TD] [/TD]
[TD] [/TD]
[/TR]
[TR]
[TD]1/4 1 layer e glass[/TD]
[TD]34[/TD]
[TD]12.0[/TD]
[TD]75.0[/TD]
[TD]87.0[/TD]
[TD]64.7%[/TD]
[TD]81.0%[/TD]
[TD] [/TD]
[TD] [/TD]
[/TR]
[TR]
[TD]1/4 2 layers 4 ounce s glass[/TD]
[TD]35[/TD]
[TD]12.0[/TD]
[TD]50.0[/TD]
[TD]62.0[/TD]
[TD]46.1%[/TD]
[TD]83.3%[/TD]
[TD] [/TD]
[TD] [/TD]
[/TR]
[TR]
[TD]1/4 1 layer carbon[/TD]
[TD]36[/TD]
[TD]12.0[/TD]
[TD]107.5[/TD]
[TD]119.5[/TD]
[TD]88.8%[/TD]
[TD]85.7%[/TD]
[TD] [/TD]
[TD] [/TD]
[/TR]
[TR]
[TD]1/4 1 layer carbon, 1 layer e glass[/TD]
[TD]40[/TD]
[TD]12.0[/TD]
[TD]135.0[/TD]
[TD]147.0[/TD]
[TD]109.3%[/TD]
[TD]95.2%[/TD]
[TD] [/TD]
[TD] [/TD]
[/TR]
[TR]
[TD] [/TD]
[TD] [/TD]
[TD] [/TD]
[TD] [/TD]
[TD] [/TD]
[TD] [/TD]
[TD] [/TD]
[TD] [/TD]
[TD] [/TD]
[/TR]
[TR]
[TD] [/TD]
[TD] [/TD]
[TD] [/TD]
[TD] [/TD]
[TD] [/TD]
[TD] [/TD]
[TD] [/TD]
[TD] [/TD]
[TD] [/TD]
[/TR]
[TR]
[TD]Stringer Stress Test **[/TD]
[TD]Weight (grams)[/TD]
[TD]Base pounds of testing device[/TD]
[TD]Additional pounds[/TD]
[TD]Total pounds to failure[/TD]
[TD]Total pounds to failure relative to baseline[/TD]
[TD]Weight relative to baseline[/TD]
[TD] [/TD]
[TD] [/TD]
[/TR]
[TR]
[TD] [/TD]
[TD] [/TD]
[TD] [/TD]
[TD] [/TD]
[TD] [/TD]
[TD] [/TD]
[TD] [/TD]
[TD] [/TD]
[TD] [/TD]
[/TR]
[TR]
[TD]Baseline - 0.75 x 0.75 plain cedar[/TD]
[TD]48[/TD]
[TD]22.0[/TD]
[TD]390[/TD]
[TD]412.0[/TD]
[TD]100.0%[/TD]
[TD]100%[/TD]
[TD] [/TD]
[TD] [/TD]
[/TR]
[TR]
[TD] [/TD]
[TD] [/TD]
[TD] [/TD]
[TD] [/TD]
[TD] [/TD]
[TD] [/TD]
[TD] [/TD]
[TD] [/TD]
[TD] [/TD]
[/TR]
[TR]
[TD]Samples[/TD]
[TD] [/TD]
[TD] [/TD]
[TD] [/TD]
[TD] [/TD]
[TD] [/TD]
[TD] [/TD]
[TD] [/TD]
[TD] [/TD]
[/TR]
[TR]
[TD]0.5 x 0.5 plain cedar[/TD]
[TD]22[/TD]
[TD]22.0[/TD]
[TD]145[/TD]
[TD]167.0[/TD]
[TD]41.5%[/TD]
[TD]45.8%[/TD]
[TD] [/TD]
[TD] [/TD]
[/TR]
[TR]
[TD]0.5 x 0.5 cedar 2 layers of carbon sleeve[/TD]
[TD]43[/TD]
[TD]22.0[/TD]
[TD]250[/TD]
[TD]272.0[/TD]
[TD]67.7%[/TD]
[TD]89.6%[/TD]
[TD] [/TD]
[TD] [/TD]
[/TR]
[TR]
[TD]0.5 x 0.75 plain cedar[/TD]
[TD]32[/TD]
[TD]22.0[/TD]
[TD]215[/TD]
[TD]237.0[/TD]
[TD]59.0%[/TD]
[TD]66.7%[/TD]
[TD] [/TD]
[TD] [/TD]
[/TR]
[TR]
[TD]0.5 x 0.75 cedar 1 layer of carbon sleeve[/TD]
[TD]46[/TD]
[TD]22.0[/TD]
[TD]300[/TD]
[TD]322.0[/TD]
[TD]80.1%[/TD]
[TD]95.8%[/TD]
[TD] [/TD]
[TD] [/TD]
[/TR]
[TR]
[TD]0.5 x 0.6 Corecell A500 foam[/TD]
[TD]9[/TD]
[TD]22.0[/TD]
[TD] [/TD]
[TD]22.0[/TD]
[TD]5.5%[/TD]
[TD]18.8%[/TD]
[TD] [/TD]
[TD] [/TD]
[/TR]
[TR]
[TD]0.5 x 0.6 Corecell A500 2 layers of carbon sleeve[/TD]
[TD]33[/TD]
[TD]22.0[/TD]
[TD]75[/TD]
[TD]97.0[/TD]
[TD]24.1%[/TD]
[TD]68.8%[/TD]
[TD] [/TD]
[TD] [/TD]
[/TR]
[TR]
[TD] [/TD]
[TD] [/TD]
[TD] [/TD]
[TD] [/TD]
[TD] [/TD]
[TD] [/TD]
[TD] [/TD]
[TD] [/TD]
[TD] [/TD]
[/TR]
[TR]
[TD] [/TD]
[TD="colspan: 7"]* Baltic Birch (1/8 and 1/4 inch thickness, 1x10 inch samples) with selected carbon fibre and fibreglass laminations (6 ounce/sq. yd. carbon and e glass cloth, laminated top and bottom, with exception of one test of 4 ounce s glass as noted for 1/4 inch plywood ), test weight applied on mid point of flat face of samples, across 8 inch span[/TD]
[TD] [/TD]
[/TR]
[TR]
[TD] [/TD]
[TD="colspan: 7"]** Stringer stress test - 12 inch long samples using 8.9 ounce biaxial carbon fibre tubular sleeve (0.75” diameter) as indicated, test weight applied at mid point on edge of widest dimension, across 6 inch span[/TD]
[TD] [/TD]
[/TR]
[TR]
[TD] [/TD]
[TD="colspan: 7"] [/TD]
[TD] [/TD]
[/TR]
[TR]
[TD] [/TD]
[TD="colspan: 7"] [/TD]
[TD] [/TD]
[/TR]
[TR]
[TD] [/TD]
[TD="colspan: 7"] [/TD]
[TD] [/TD]
[/TR]
[TR]
[TD] [/TD]
[TD="colspan: 7"] [/TD]
[TD] [/TD]
[/TR]
[TR]
[TD] [/TD]
[TD="colspan: 7"] [/TD]
[TD] [/TD]
[/TR]
[TR]
[TD] [/TD]
[TD="colspan: 7"] [/TD]
[TD] [/TD]
[/TR]
[TR]
[TD] [/TD]
[TD="colspan: 7"] [/TD]
[TD] [/TD]
[/TR]
[TR]
[TD] [/TD]
[TD="colspan: 7"] [/TD]
[TD] [/TD]
[/TR]
[TR]
[TD] [/TD]
[TD="colspan: 7"] [/TD]
[TD] [/TD]
[/TR]
[/TABLE]
Attachments
Last edited: