Update on this rebuild ...
Things were going great until they weren't. I made up a set of thwarts (more on that later), guestimated where to put them, cut them to length so the boat would be 26.5 wide, applied copious quantities of spar urethane, and installed them. Everything looked great! Then I picked it up and swung it around as one might while car topping etc and heard a loud CRACK. Upon examination, it turned out one of the outwale scarfs had partly failed. Much swearing commenced. I don't even have a picture because I was too pissed.
The fact that I used a 9' board for ~16' 4" rails meant that I didn't have that much choice in terms of where the scarfs ended up. I've done a lot of epoxy work on hulls, but this was my first set of scarfs, and it seems I scored 75%. It doesn't help that on this particular hull the outwale is under a lot of strain since the correct/spec shape of the boat is much narrower than the relaxed state. Still, knowing all this I probably should have at least upsized the outwales a bit (they are 3/4 x 3/4, same as the inwales). Also, a horizontal orientation of the scarfs would have been better. I had to admit that a decent drywall monkey would not have screwed this up. Maybe this humility will do me good.
It wasn't a fatal failure and I was able to repair it in situ, but I did feel the need to add a bit of support in the form of a bolt at that point, which is an aesthetic flaw. More humility.
Here's a pic of the rescue -- "save the outwhales!". Straps are holding it to maintain spec width/tumblehome.
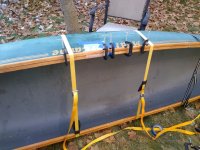
(As an aside, the more I hang out on this board the more clamps I think I need.)
On the bright side, the outfitting is coming along nicely. When I ripped the gunwales I ended up with a strip of poplar about 1.25" wide left over. It looked about thwart sized to me, and this boat didn't come with any (non ad-hoc) thwarts. However, test bending it it didn't seem quite up to the task. However, I was already in ripping mode, and it occurred to me that with a bit of hardwood laminated in that almost-thwart would be plenty strong. I looked around the scraps in my cellar and found a clear piece of maple left over from a kitchen remodel (15 years ago). It was hard as a rock, but I ripped some 1/4" strips out of it and made ice cream sandwiches with the softer poplar.
Making the thwarts -- I could have used more clamps.
I had to do quite a bit of planing/sanding, being careful not to carve too deeply into the soft "ice cream" but they turned out well, light (less than a pound for both of them) and quite strong to my knee. I liked them so much I did the same thing for the grab handles, only they're one 1/4" maple strip with 3/4" poplar (used end scraps from the rails).
Here's the boat in a more or less operational state (sorry for the lack of focus)
Detail on the seat/thwart
With the boat in it's correct shape you can see the chines. I know this is a Jim Henry design, but it strikes me as Jenseny.
I consider these soft gunwales on probation, I may later need to upgrade them or at least the outwales. Still, this rebuild is far enough along that I know the hull is valid and that the shearline flare issue is solvable without drastic measures. For now, the opera singer's corset is holding.
Still a lot more work to do:
Sliding seat tweaks
Float chambers
Decks?
Liberating the bow from Bondo