G
Guest
Guest
I don’t know nothing ‘bout no foam core material, stuff like the stiffening diamonds laminated on the bottom of some UL canoes.
But I’m off on a tangent to build a couple of ultra-light blue barrel folding tabletops. Which, since I am far from a light packer, is kinda silly, and probably more proof of concept than anything else. But I can give the UL Mark III and IV experiments away to tripper friends for field testing.
I think I have a line on some corrugated kevlar honeycomb, but would also like to try my hand at DIY laminating some foam core material, covered with S-glass, epoxy and peel ply.
My preferred barrel tabletop shape is this “squared circle”, hinged in the middle, rounded off from two pieces of +/- 10x20 material.
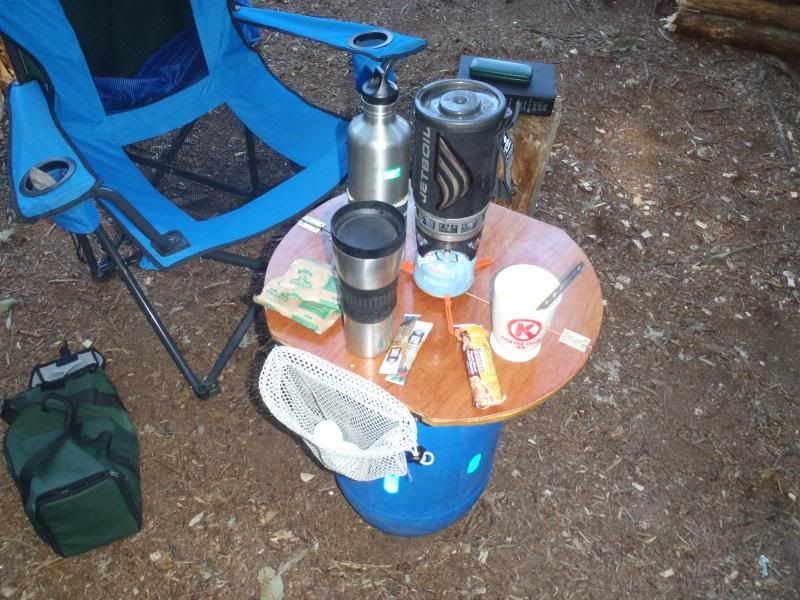
That size works well dimensionally as a 30L solo table, and I know I can save weight on the hinges, and on the lid-sized donut circle stabilizer underneath, which could be economically cut from lightweight minicel exercise foam. I think I can get the “hinge” and underside donut down to a couple ounces at most, so it is mostly the weight of the platform itself.
This sucks for anything but the most minimalist kitchen countertop. Never again.

So, some foam core newbie questions:
What is that foam? Who sells it as a US supplier?
Does epoxy & glass application adhere well to that foam without any fancy footwork vacuum bagging/infusion type tricks? I want a smooth (glass, peel ply, light sanding, varnish topcoat) washable kitchen counter.
Is that foam core available in different thickness? Half inch thick material would be butt-ends-hinged helpful to maintain a no-droop surface. Or maybe two thinner pieces of foam laminated together?
Thoughts on whether that foam core material be stiff enough, laminated with a couple layers of epoxied S-glass layers top and bottom, to maintain a flat surface extending out 10 inches from the barrel lid circumference and not droop on the sides with meal prep weight? The flush center of the tabletop is already sturdily supported on the 10 inch diameter of the 30L barrel lid underneath.
Even with my shade tree skills I want to see if I can get a blue barrel folding tabletop weight under 1lb. And I’d like to try my hand at making a larger one for the 60L barrel.
Tell me about foam core.
But I’m off on a tangent to build a couple of ultra-light blue barrel folding tabletops. Which, since I am far from a light packer, is kinda silly, and probably more proof of concept than anything else. But I can give the UL Mark III and IV experiments away to tripper friends for field testing.
I think I have a line on some corrugated kevlar honeycomb, but would also like to try my hand at DIY laminating some foam core material, covered with S-glass, epoxy and peel ply.
My preferred barrel tabletop shape is this “squared circle”, hinged in the middle, rounded off from two pieces of +/- 10x20 material.
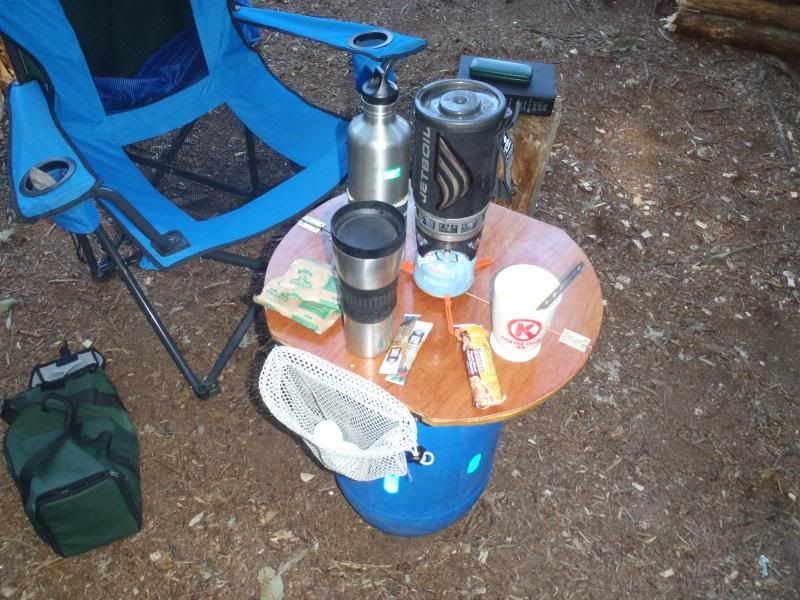
That size works well dimensionally as a 30L solo table, and I know I can save weight on the hinges, and on the lid-sized donut circle stabilizer underneath, which could be economically cut from lightweight minicel exercise foam. I think I can get the “hinge” and underside donut down to a couple ounces at most, so it is mostly the weight of the platform itself.
This sucks for anything but the most minimalist kitchen countertop. Never again.

So, some foam core newbie questions:
What is that foam? Who sells it as a US supplier?
Does epoxy & glass application adhere well to that foam without any fancy footwork vacuum bagging/infusion type tricks? I want a smooth (glass, peel ply, light sanding, varnish topcoat) washable kitchen counter.
Is that foam core available in different thickness? Half inch thick material would be butt-ends-hinged helpful to maintain a no-droop surface. Or maybe two thinner pieces of foam laminated together?
Thoughts on whether that foam core material be stiff enough, laminated with a couple layers of epoxied S-glass layers top and bottom, to maintain a flat surface extending out 10 inches from the barrel lid circumference and not droop on the sides with meal prep weight? The flush center of the tabletop is already sturdily supported on the 10 inch diameter of the 30L barrel lid underneath.
Even with my shade tree skills I want to see if I can get a blue barrel folding tabletop weight under 1lb. And I’d like to try my hand at making a larger one for the 60L barrel.
Tell me about foam core.