Infusion looks pretty neat so I thought I'd give it a go. I'm already set up for vacuum bagging so I didn't have to buy much for supplies to do infusion as well. It's similar in that everything is sealed up in a bag under vacuum but with infusion everything is set up and the bag sealed when dry. After it's sealed you pull a vacuum and then suck the resin in. Pretty nifty and I really liked the thought of working with dry cloth as opposed to wet and not having to get the bag sealed up while everything is smeared with resin.
Last night was the first run. Some carbon over foam sliding seat braces and a thwart and grab handle. At the last minute I pulled some other seat components out because there wasn't much room and I decided if it all went south I didn't want to have to remake them. I got some vinyl ester resin just for this because it's thinner and cheaper. I don't like the smell but that should mostly stay contained in the bag.
Things started off like they normally do in my shop when I started mixing the resin in my standard plastic dixie cup. Something felt sticky in the bottom of the cup while I was stirring it. Then the cup started to turn a funny color. Oh crap, it's gonna eat through! Hurry up and set it outside before it dumps all over the floor. Of course I now realize, in hindsight, that was a giant red flag, but at the time I had about a million things on my mind so I let it slide. At least that's my excuse. Grabbed a more industrial rated cup and proceeded to mix another batch.
So the vacuum is pulled, it's holding well, and it's finally time for the big moment. Open up the clamp and let the resin get sucked in. I anxiously watch the front line as it slowly advances across the bag, wetting out each piece in turn. It's like magic. It looks just like all the videos on the interwebs. It's beautiful! When it reaches the opposite side I clamp off the resin line and look at my grab handle, which was the first part the resin contacted. Hmmm, looks kinda funny. What the heck is going on here? Oh mother %$#!*&$%! That danged vinyl ester resin is eating the XPS foam! Shut off the vacuum pump, kill the lights, and go back in the house. Two and a half hours down the tube with every piece ruined and my shop smells terrible. Good thing I have a sense or humor. I was still chuckling about it when I went to bed.
So I'm calling test #1 a complete success. I learned a valuable lesson that I won't be repeating anytime soon. Just to be sure this grab handle will be hanging on the wall as a reminder:
20160216_002 by Alan, on Flickr
Alan
Last night was the first run. Some carbon over foam sliding seat braces and a thwart and grab handle. At the last minute I pulled some other seat components out because there wasn't much room and I decided if it all went south I didn't want to have to remake them. I got some vinyl ester resin just for this because it's thinner and cheaper. I don't like the smell but that should mostly stay contained in the bag.
Things started off like they normally do in my shop when I started mixing the resin in my standard plastic dixie cup. Something felt sticky in the bottom of the cup while I was stirring it. Then the cup started to turn a funny color. Oh crap, it's gonna eat through! Hurry up and set it outside before it dumps all over the floor. Of course I now realize, in hindsight, that was a giant red flag, but at the time I had about a million things on my mind so I let it slide. At least that's my excuse. Grabbed a more industrial rated cup and proceeded to mix another batch.
So the vacuum is pulled, it's holding well, and it's finally time for the big moment. Open up the clamp and let the resin get sucked in. I anxiously watch the front line as it slowly advances across the bag, wetting out each piece in turn. It's like magic. It looks just like all the videos on the interwebs. It's beautiful! When it reaches the opposite side I clamp off the resin line and look at my grab handle, which was the first part the resin contacted. Hmmm, looks kinda funny. What the heck is going on here? Oh mother %$#!*&$%! That danged vinyl ester resin is eating the XPS foam! Shut off the vacuum pump, kill the lights, and go back in the house. Two and a half hours down the tube with every piece ruined and my shop smells terrible. Good thing I have a sense or humor. I was still chuckling about it when I went to bed.
So I'm calling test #1 a complete success. I learned a valuable lesson that I won't be repeating anytime soon. Just to be sure this grab handle will be hanging on the wall as a reminder:
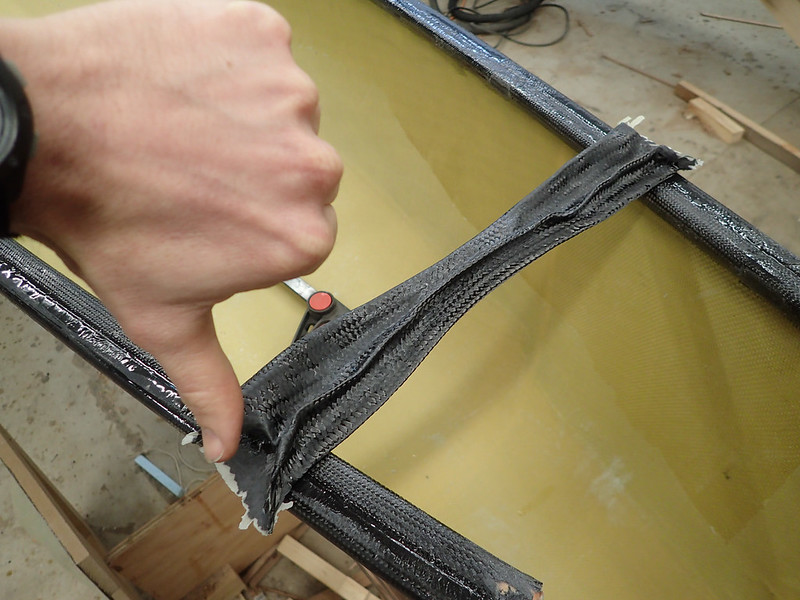
Alan