So here’s an update. Following up on lashing the gore ends closed, I scarfed and epoxied into place the two cherry wood inwales - pretty straightforward process, but note the 25 pound plate on the plywood to prevent it from tipping over on me due to the weight of all the clamps (don’t ask how I found out that this was necessary).
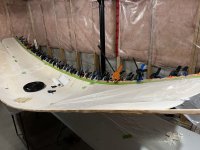
Then I wrapped the plywood in a bunch of short cam straps and began to tighten them up gradually, after wetting the bottom of the plywood with hot water and a paint brush. Again, a very straightforward process that took me maybe a half hour overall, and resulted in a very canoe-like hull.
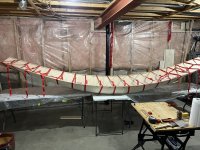
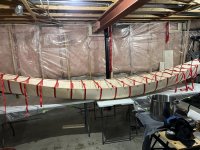
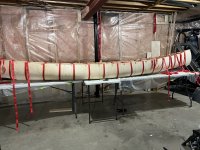
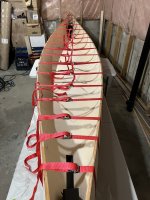
Only one small fracture in the plywood at the end of it all, resulting I think from some blow-out of the outer ply layer from sloppy drilling of the hole through the hull at the end of this particular gore. Easily fixed with a dab of epoxy and a couple of tiny screws to clamp it shut. I also got some dye bleed on the exterior from the wet hull and cheap cam straps I used, but again no big deal.
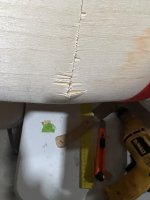
I then secured the joins at each end with thickened epoxy and some 4 ounce fiberglass inside the stems, and aligned and filled whatever openings remained in the gores.

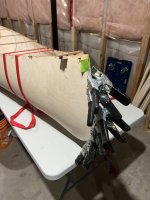
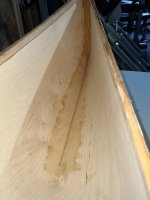

At this stage the hull is already very smooth, nicely faired with gentle curves, and really needs only a little bit of touch up sanding here and there on the ends and gores before it can be glassed. Amazingly fast process overall that I am confident could be done in well under two weeks from start to finish, including fibreglass and varnish, if you put in more than an hour or two per day. Weight right now including the inwales and ribs discussed below is 20.25 pounds - I should wind up somewhere in the 30 pound range overall, while I expect the Baltic Birch core under fibreglass will be very tough.
But there are some downsides: first, this makes for a pretty flat bottomed canoe throughout the middle third, which needs to be kept in mind depending on how it is to be used. When I glass it I think I can push the bottom out to get a little rounding, but likely not much.
Second, I wound up with quite a bit more rocker than I would normally shoot for - probably 3 inches or so near the stems, after a steady rise from the middle. I think some of this is inherent in the build technology but is also in part due to me not paying enough attention to how wide I cut the gores (a couple of mm wider than the plan calls for in the middle probably translates into quite a bit more height at the ends once it is all closed up).
Third, at the bottom ends of the gores in the middle there is a little pucker in the plywood that leads to a series of 4 little bumps in the hull along each side (roughly at the waterline). As far as I can tell this is pretty well unavoidable. Some builders of these boats have apparently sanded these bumps flat and reinforced them from the inside with epoxy. I don’t think they are serious enough for that, and I will probably leave them alone, as they are not really noticeable unless you look for them.
And finally, while also not a big deal, I don’t like the look of the gores and plywood seams on the canoe (I will be painting the outside, so this is only an issue for the interior). So I decided to add some ribs to cover all the seams. Not having worked with steam bending before, I spent the better part of a week messing around with various options before settling on some thin cherry ribs (1/8 by 1 inch) that seemed acceptable. As these are mostly cosmetic given their thinness, I may also add some half ribs in the centre third to help out with any potential oil canning along the flat part of the bottom if that becomes an issue. These are just bent and laid into place for now, and will be epoxied in after the interior fibreglass.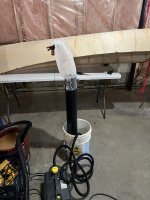
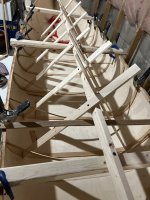
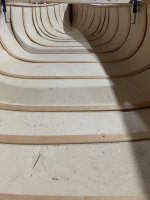
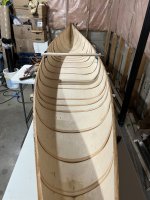
So that’s about it for now - no “hot mess” and seems like it will be a pretty decent little canoe overall.
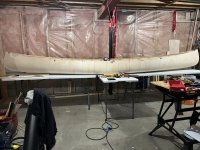
I will have to wait for spring before I can (hopefully) squeeze this out my basement window and into the garage for fibreglassing and final finishing. Will provide an update on the final product then. In the meantime, now that I have my personal “proof of concept“ so to speak, I have to find a way to deal with the divinycell earbug that Stripperguy has planted in my mind - I know I want one, but do I really need a 20 pound canoe?.
Thanks all
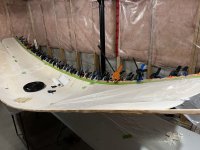
Then I wrapped the plywood in a bunch of short cam straps and began to tighten them up gradually, after wetting the bottom of the plywood with hot water and a paint brush. Again, a very straightforward process that took me maybe a half hour overall, and resulted in a very canoe-like hull.
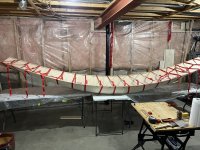
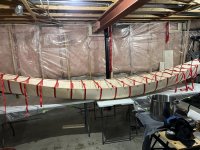
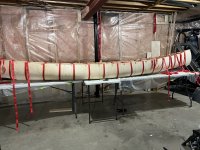
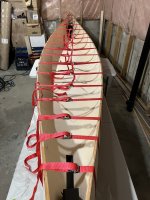
Only one small fracture in the plywood at the end of it all, resulting I think from some blow-out of the outer ply layer from sloppy drilling of the hole through the hull at the end of this particular gore. Easily fixed with a dab of epoxy and a couple of tiny screws to clamp it shut. I also got some dye bleed on the exterior from the wet hull and cheap cam straps I used, but again no big deal.
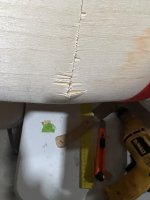
I then secured the joins at each end with thickened epoxy and some 4 ounce fiberglass inside the stems, and aligned and filled whatever openings remained in the gores.

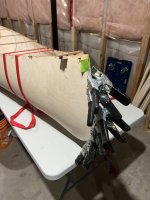
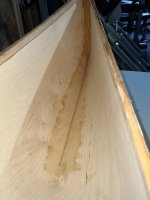

At this stage the hull is already very smooth, nicely faired with gentle curves, and really needs only a little bit of touch up sanding here and there on the ends and gores before it can be glassed. Amazingly fast process overall that I am confident could be done in well under two weeks from start to finish, including fibreglass and varnish, if you put in more than an hour or two per day. Weight right now including the inwales and ribs discussed below is 20.25 pounds - I should wind up somewhere in the 30 pound range overall, while I expect the Baltic Birch core under fibreglass will be very tough.
But there are some downsides: first, this makes for a pretty flat bottomed canoe throughout the middle third, which needs to be kept in mind depending on how it is to be used. When I glass it I think I can push the bottom out to get a little rounding, but likely not much.
Second, I wound up with quite a bit more rocker than I would normally shoot for - probably 3 inches or so near the stems, after a steady rise from the middle. I think some of this is inherent in the build technology but is also in part due to me not paying enough attention to how wide I cut the gores (a couple of mm wider than the plan calls for in the middle probably translates into quite a bit more height at the ends once it is all closed up).
Third, at the bottom ends of the gores in the middle there is a little pucker in the plywood that leads to a series of 4 little bumps in the hull along each side (roughly at the waterline). As far as I can tell this is pretty well unavoidable. Some builders of these boats have apparently sanded these bumps flat and reinforced them from the inside with epoxy. I don’t think they are serious enough for that, and I will probably leave them alone, as they are not really noticeable unless you look for them.
And finally, while also not a big deal, I don’t like the look of the gores and plywood seams on the canoe (I will be painting the outside, so this is only an issue for the interior). So I decided to add some ribs to cover all the seams. Not having worked with steam bending before, I spent the better part of a week messing around with various options before settling on some thin cherry ribs (1/8 by 1 inch) that seemed acceptable. As these are mostly cosmetic given their thinness, I may also add some half ribs in the centre third to help out with any potential oil canning along the flat part of the bottom if that becomes an issue. These are just bent and laid into place for now, and will be epoxied in after the interior fibreglass.
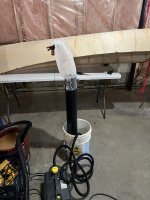
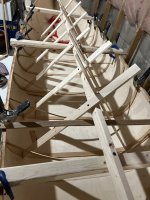
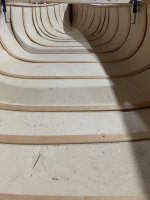
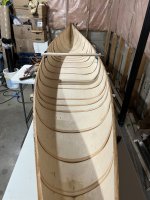
So that’s about it for now - no “hot mess” and seems like it will be a pretty decent little canoe overall.
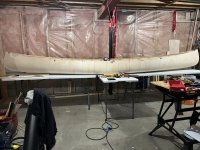
I will have to wait for spring before I can (hopefully) squeeze this out my basement window and into the garage for fibreglassing and final finishing. Will provide an update on the final product then. In the meantime, now that I have my personal “proof of concept“ so to speak, I have to find a way to deal with the divinycell earbug that Stripperguy has planted in my mind - I know I want one, but do I really need a 20 pound canoe?.
Thanks all
Last edited: