Maybe it's still my eyes or the camera playing tricks on me but those dark spots really look like holes in the weave. Not that there might not be dirt trapped in there as well but it looks like more than just the exposed texture of the weave. When I think of saturated cloth with exposed weave I think of a stripper just after it's been wetted out. The weave of the cloth is very obvious and pronounced but the depression between the weaves is filled in solid. Dirt would be harder to remove than normal but should be doable.
Starved cloth may or may not show the texture of the weave but in the depression between the weaves it shows a small hole rather than a solid depression. In either case more epoxy is probably the best course of action but in the case of starved cloth with pinholes in the weave in can be difficult to fill those with regular epoxy. The epoxy can be too thick to flow into the void and allow the air to escape. Often times I'll brush/roll the epoxy on and everything will look fine and then next time I turn around it burped a little air bubble and pushed the epoxy out of the hole. Then it's too thick to flow back in by itself.
I've had good luck using an ultra thin epoxy that wasn't much thicker than vinylester resin. It seemed to soak right into those little holes. I've also had good luck using thickened epoxy applied with a squeegee so that you're really forcing it down into those holes. Both those seemed to work better than straight epoxy.
This has fully wetted out cloth with exposed weave. More epoxy and sanding is the easy way to fill it:
20150309_004 by Alan, on Flickr
This cloth was badly starved. It did a good job sucking up a very thin epoxy. Regular epoxy probably wouldn't have worked so well:
20160104_009 by Alan, on Flickr
Alan
Starved cloth may or may not show the texture of the weave but in the depression between the weaves it shows a small hole rather than a solid depression. In either case more epoxy is probably the best course of action but in the case of starved cloth with pinholes in the weave in can be difficult to fill those with regular epoxy. The epoxy can be too thick to flow into the void and allow the air to escape. Often times I'll brush/roll the epoxy on and everything will look fine and then next time I turn around it burped a little air bubble and pushed the epoxy out of the hole. Then it's too thick to flow back in by itself.
I've had good luck using an ultra thin epoxy that wasn't much thicker than vinylester resin. It seemed to soak right into those little holes. I've also had good luck using thickened epoxy applied with a squeegee so that you're really forcing it down into those holes. Both those seemed to work better than straight epoxy.
This has fully wetted out cloth with exposed weave. More epoxy and sanding is the easy way to fill it:
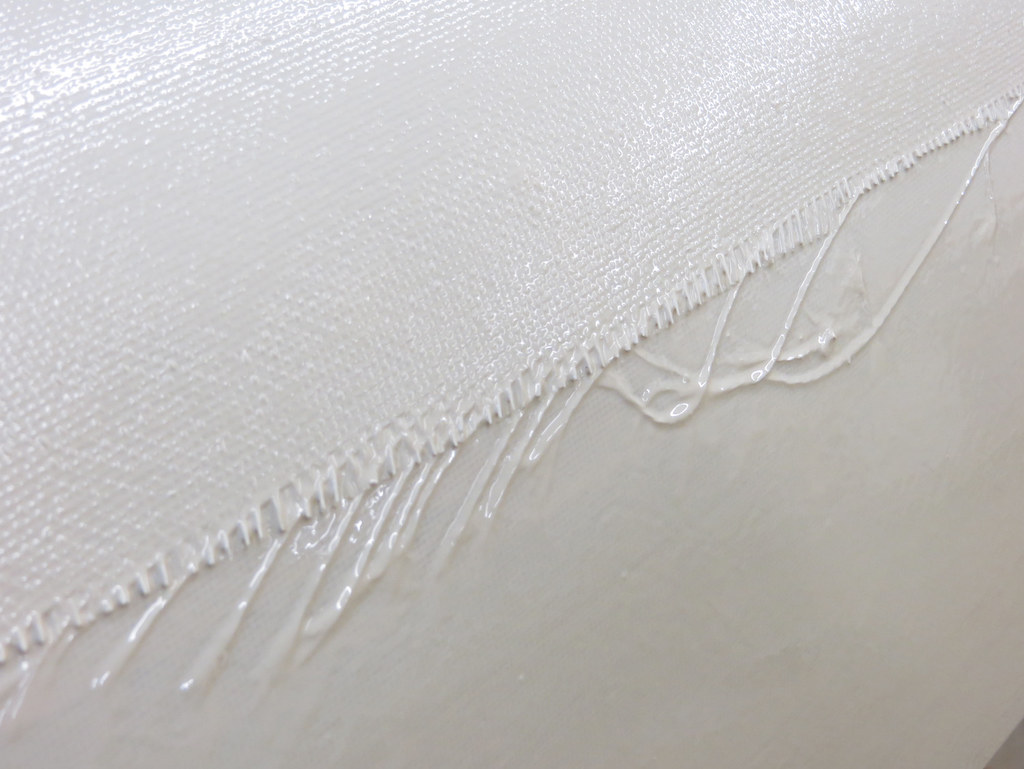
This cloth was badly starved. It did a good job sucking up a very thin epoxy. Regular epoxy probably wouldn't have worked so well:
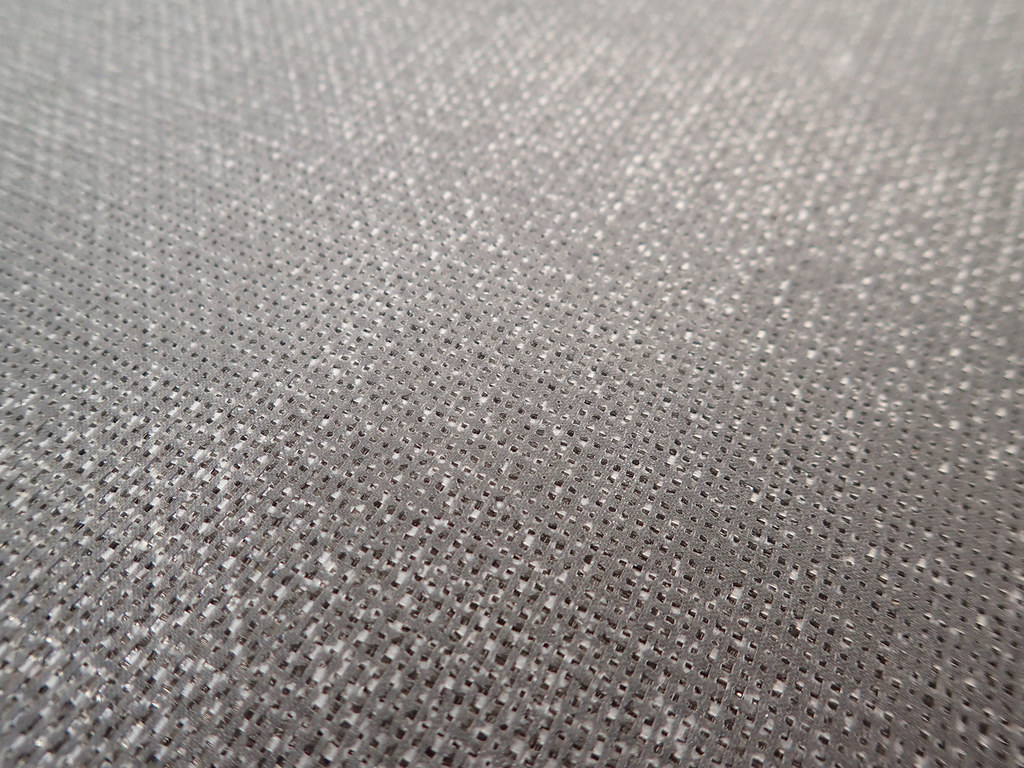
Alan