Too late to change my mind on anything now. The first four layers are down. Full layer of fiberlass, full layer of Kevlar, carbon reinforcements and another layer of Kevlar below the waterline. Four more layers tomorrow and then all I can do is wait and hope it releases.
Last minute decision to keep the ends open rather than closed thanks to some input from Jim Dodd and Muskrat. No core on this build. I've got a sneaking suspicion it's not going to be quite stiff enough. If that's the case I'll add more layers to the inside.
I'm trying to keep all the Kevlar away from the stems and shear so I won't have to try cutting/grinding it after it's cured. Trimming the kevlar ahead of time and properly placing it over a wet layer seemed like a disaster so I put on both of the first two layers dry, trimmed the Kevlar, and wetted them out together.
Things went well tonight and I'm feeling pretty good about it.
Here it is waxed with 3 layers of PVA sprayed on. Also tape along the stems to keep them open and along the shear so that it will at least be free there if I need to use shims to un-stick it.
20151210_002 by Alan, on Flickr
6oz glass:
20151210_003 by Alan, on Flickr
Ran short and had to add some patches. Light mist of contact adhesive held them in place nicely:
20151210_004 by Alan, on Flickr
Now a layer of 6oz Kevlar. Both layers dry at this point:
20151210_005 by Alan, on Flickr
Taking a break for fresh gloves and new roller and mixing pot. Carbon reinforcements nearly wetted out:
20151210_006 by Alan, on Flickr
And finally a layer of Kevlar below the water line:
20151211_009 by Alan, on Flickr
Stuck some peel ply on the rough edges to hopefully tame them a little before adding more layers tomorrow:
20151211_012 by Alan, on Flickr
Alan
Last minute decision to keep the ends open rather than closed thanks to some input from Jim Dodd and Muskrat. No core on this build. I've got a sneaking suspicion it's not going to be quite stiff enough. If that's the case I'll add more layers to the inside.
I'm trying to keep all the Kevlar away from the stems and shear so I won't have to try cutting/grinding it after it's cured. Trimming the kevlar ahead of time and properly placing it over a wet layer seemed like a disaster so I put on both of the first two layers dry, trimmed the Kevlar, and wetted them out together.
Things went well tonight and I'm feeling pretty good about it.
Here it is waxed with 3 layers of PVA sprayed on. Also tape along the stems to keep them open and along the shear so that it will at least be free there if I need to use shims to un-stick it.

6oz glass:
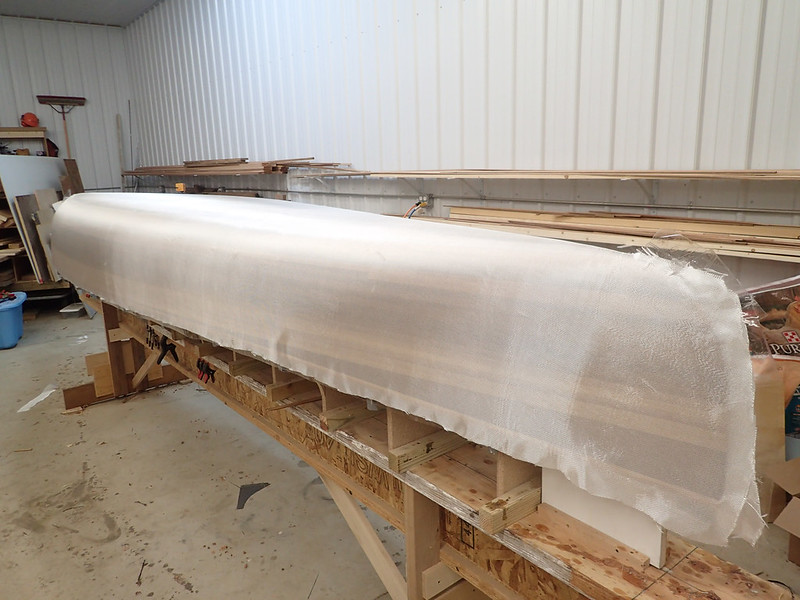
Ran short and had to add some patches. Light mist of contact adhesive held them in place nicely:
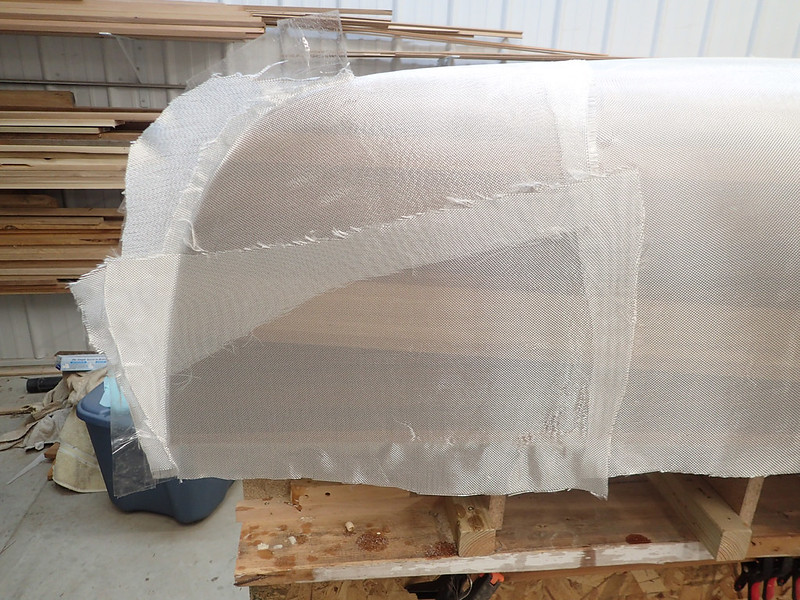
Now a layer of 6oz Kevlar. Both layers dry at this point:

Taking a break for fresh gloves and new roller and mixing pot. Carbon reinforcements nearly wetted out:

And finally a layer of Kevlar below the water line:
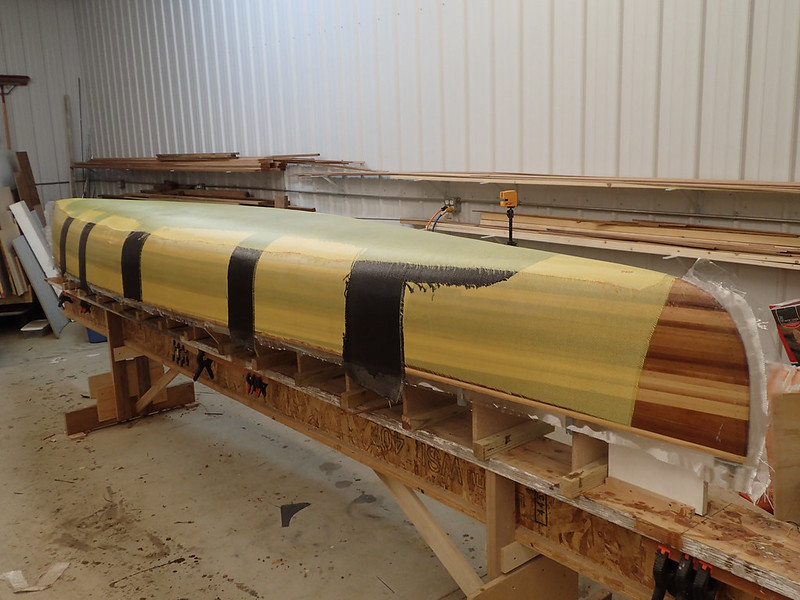
Stuck some peel ply on the rough edges to hopefully tame them a little before adding more layers tomorrow:
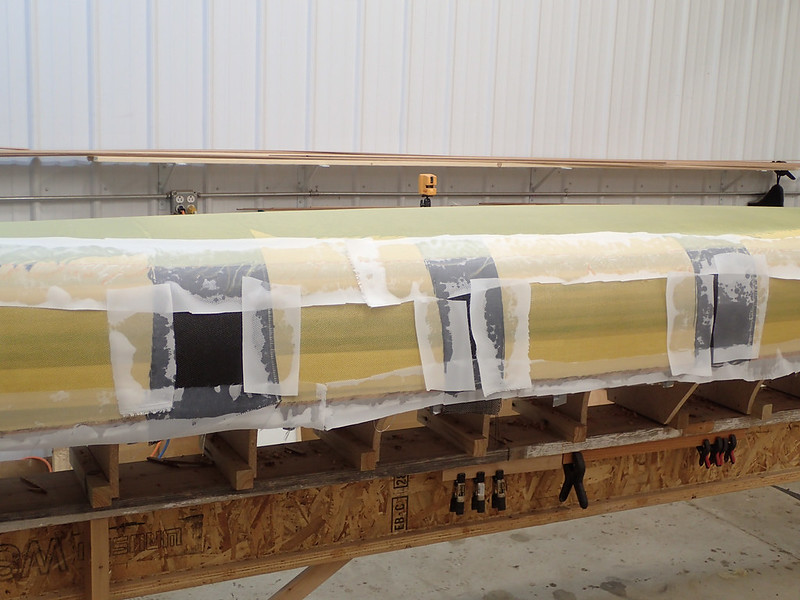
Alan